For novel process technologies, each development stage brings new safety obligations. This guide provides a practical framework for navigating safety responsibilities from early R&D to commercialization
Developing new process technologies — especially those involving hazardous materials or operations at high pressures or temperatures — can be an exciting journey of innovation. But it’s also one that comes with serious safety responsibilities. Whether you are working on a novel chemical process, a sustainable fuel pathway or a next-generation material, safety must evolve with your technology.
In addition to the technical challenges of development, new technology developers — particularly those spinning out from universities — must also come to grips with a new set of responsibilities around safety. Unlike academic environments, where the focus is often on discovery and proof of concept, the transition to commercialization introduces regulatory, operational and legal (safety) obligations that may be unfamiliar (Figure 1). This can be a steep learning curve. Understanding what you need to know, what actions you need to take at each stage, and how to prioritize safety alongside innovation can be daunting. Often, developers must learn as they go.
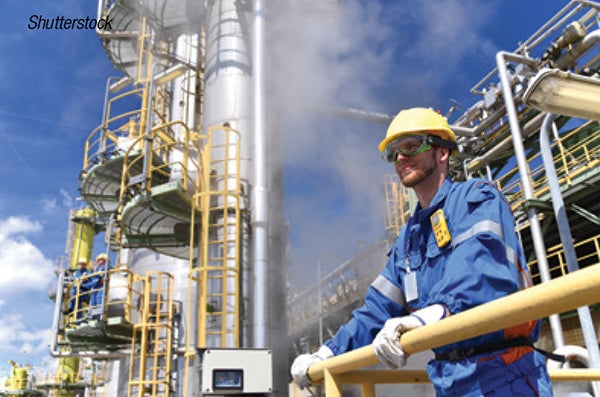
FIGURE 1. Transitions from technology development to commercialization introduce different regulatory and safety obligations for operators
This article provides a stage-by-stage guide to managing safety across the technology readiness levels (TRLs), with a practical focus for startups, scale-ups and research and development (R&D) organizations.
TRLs in process technology
Technology readiness levels are a framework used to describe the maturity of a technology, from initial concept through to full commercial deployment. Originally developed by the U.S. National Aeronautics and Space Administration (NASA; www.nasa.gov) to assess the readiness of space-related technologies, TRLs have subsequently been widely adopted across industries — including the chemical process industries (CPI) — as a structured way to evaluate how far a technology has progressed.
In the process industries, TRLs are particularly useful for understanding the level of technological development, which can help align expectations and decisions around grant funding, private investment and innovation support. Identifying the TRL that a technology has reached helps developers and stakeholders more clearly communicate progress, anticipate technical challenges and assess risks.
TRLs are divided into nine levels (Figure 2). Each stage in the TRL process increases the complexity, intensity and scale of a technology, and at each stage, new types of safety risks emerge. These range from handling larger quantities of hazardous materials to operating under higher pressures or temperatures. The controls implemented must evolve accordingly, becoming more robust and systematic as the technology develops.
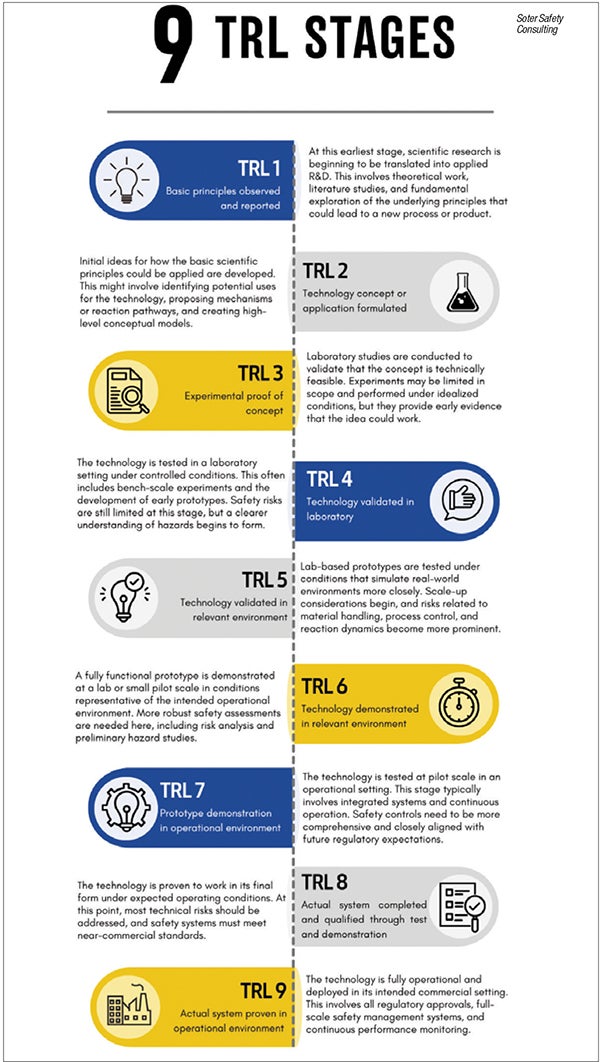
FIGURE 2. Technology readiness levels (TRLs) describe the maturity of a technology and are numbered according to a framework developed by NASA
Safety at Every TRL
Before diving into each TRL stage, it is important to recognize that in practice, TRLs do not always follow a clean, linear path. Technologies often move fluidly between levels, with activities overlapping and transitions blurring. The same is true for safety considerations: they don’t jump sharply from one TRL to the next, but instead evolve with the scale and complexity of the operations. Often, the most significant shifts in safety management occur not between TRLs, but when moving from a theoretical idea to a physical process, or from laboratory to pilot scale. What follows are safety considerations for each of the 9 TRLs.
TRL 1–2: Early R&D
At this stage, work is mostly theoretical — focused on exploring fundamental principles and forming the basis of a technological concept. While there may be little or no physical process to manage yet, there is an opportunity to embed safety into the design philosophy and establish a safety-first mindset. This means actively shaping research and planning with future safety implications in mind. For example,
• Start thinking about what materials you might use and whether they pose safety risks, such as toxicity, reactivity or flammability
• Consider whether the process might involve high pressures, extreme temperatures or other hazardous operating conditions
• Design technology with safety scalability in mind — think about how will it behave, not just in a test tube, but also in a reactor
By integrating these considerations early, the engineering team will tend to make smarter technical choices, avoid rework later and demonstrate to funders, investors and employees that the responsibility to create a safe working environment is clearly understood, and the organization is committed to achieving this goal.
Common challenges (and why they happen). Even though physical hazards may not yet be present, many developers fall into traps that make safety harder down the line:
• Overlooking future risks. It is easy to dismiss safety when the technology exists only on paper, but design decisions made now will carry through to scale-up.
• Delaying safety engagement. Teams may assume they can “add safety later,” but this often leads to costly redesigns or missed regulatory expectations.
These challenges usually occur because the early focus is on proof of concept, and safety can feel abstract or secondary. Changing that mindset is critical.
Managing safety risks at TRL 1–2.
• Conduct an early-stage hazard identification (HAZID). Even if speculative, mapping potential hazards sets the tone for future safety assessments.
• Identify potential hazardous materials and energy sources. Begin compiling a list of what your process might eventually involve.
• Explore regulatory implications early. For instance, if your process could eventually fall under specific regulatory requirements due to the nature or quantity of hazardous materials you are likely to produce, now is the time to find out what thresholds or classifications apply.
• Document emerging safety considerations. Capture these insights in your funding proposals and design plans — this shows foresight and builds investor confidence.
TRL 3–4: Lab bench-scale
With concept proven, developers likely begin handling real substances — perhaps performing small-batch reactions, thermal or pressure testing or initial process parameter mapping. These activities mark the transition to a working laboratory environment where risks become tangible. Your setup may be small and experimental, but the introduction of chemicals, energy and equipment means safety becomes operational, not just theoretical. At this stage, processes may be operating in a shared laboratory space, a university setting or a dedicated R&D facility. Either way, you are now responsible for managing risks in a live environment (Figure 3).
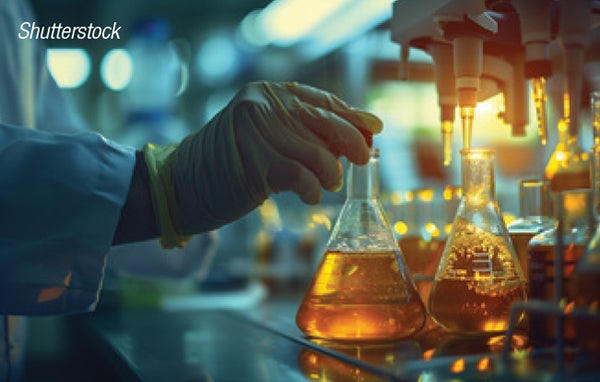
FIGURE 3. Although activities at TRL 3 are smallbatch reactions, developers are still responsible for managing risks
At TRL 3–4, several real-world hazards begin to emerge:
•Toxic or flammable chemicals that can pose inhalation or fire risks
•Exothermic or pressure-building reactions, where poor control can result in incidents
•Unexpected byproducts that may introduce new risks or require special handling
• Lone working, especially outside normal hours, which introduces additional procedural and emergency response risks.
• Use of pressurized systems, piped gases or experimental equipment that may fall under local pressure-equipment safety regulations
• Fire safety measures, which need to align with the facility’s risk profile and occupancy type.
This is also when an organization begins forming its laboratory safety culture — a critical foundation for the broader process safety culture that is required for scaleup.
Common challenges (and why they happen). At this stage, technology developers are often focused on technical success — getting experiments to work, collecting data and refining understanding of the process. Safety is recognized as important, but without formal processes in place, gaps can emerge. Here are some of the most common issues, and why they occur:
• Ad hoc safety practices. Without formal training in laboratory safety management, teams often rely on informal or inherited procedures. This can lead to inconsistencies in how risks are assessed, documented or controlled.
• Unclear regulatory expectations. Developers may not yet know which rules apply or mistakenly believe regulations only become relevant at pilot or commercial scale. This can delay critical safety measures and put funding or facility access at risk.
• Lack of documentation discipline. As experiments evolve rapidly, safety documentation is often an afterthought. This creates challenges later when you need to demonstrate due diligence, apply for permits or onboard new staff.
• Overreliance on individuals. In small teams, safety responsibilities often fall to one person — usually a founder or technical lead — who has limited time or expertise. This makes safety vulnerable to workload and turnover.
• Underestimating laboratory-scale risks. Because activities are still “small-scale,” teams may downplay hazards’ severity. However, even bench-scale processes can cause fires, injuries or environmental releases if not managed properly.
These challenges are not unusual, but they are important to recognize and proactively address. If uncertainty about how to assess or control a hazard exists at this stage, reach out to local regulatory authorities for guidance, or consider consulting a chartered safety professional.
Managing safety risks at TRL 3–4.
• Conduct a comprehensive regulatory review tailored to the jurisdiction in which the process resides. Understanding legal obligations early — covering health and safety laws, chemical safety, pressure systems and emergency response — can identify improvement opportunities and help you plan for compliance.
• Carry out detailed risk assessments for every procedure and material used. This should include risks associated with work activities as well as those from use, storage and handling of chemicals.
• Implement robust chemical management practices, including inventory tracking systems, proper labeling and segregation of hazardous materials and safe storage aligned with reactivity and stability profiles
• Develop and roll out core laboratory safety systems, including safe operating procedures, good housekeeping standards, emergency protocols, signage and personal protective equipment (PPE) requirements
• Start introducing formal systems, including a documented safety-management system and inventory control protocols, to support consistent practices and regulatory record-keeping requirements.
• Promote a strong safety culture by encouraging reporting of near misses, conducting regular laboratory walk-throughs and offering training that links safety to innovation success.
• Revisit your early-stage HAZID to identify and document any new hazards introduced as you advance to the next TRL level, while removing those that are no longer relevant. This ensures that risk knowledge stays current and aligned with evolving operations
TRL 5–6: Larger-scale testing
As a technology matures and equipment and material inventories grow, the complexity of the risks increases. At this stage, small reactors, pilot rigs or prototypes may be operating in larger laboratory spaces or dedicated test bays (Figure 4). The transition from bench-scale to prototype development introduces new challenges that require careful attention to safety processes and risk management.
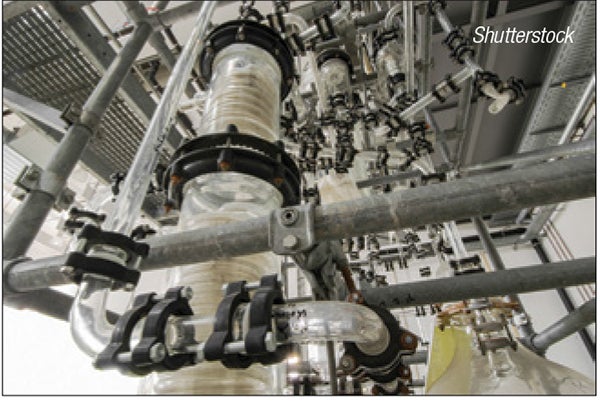
FIGURE 4. Several common safety challenges arise when scaling up technology from benchscale to prototype
At TRL 5–6, you will encounter more complex risks as you scale up operations, including the following:
• Pressure systems — High-pressure processes must be considered.
• Energy storage — Managing larger quantities of energy involves increased risk of thermal runaway or other hazards.
• Multi-step or continuous processes — As processes become more integrated and continuous, new risks arise from material and energy flow, system stability and process interactions.
This stage also brings a greater regulatory focus, and it is crucial to ensure that processes align with safety requirements at a larger scale.
Common challenges (and why they happen). As technology is scaled up from bench-scale to prototype development, several common challenges may arise. Understanding why these challenges occur can help developers navigate them effectively and ensure that safety and compliance are not compromised.
• Inadequate scaling of safety measures. As processes scale up from laboratory to larger systems, earlier safety measures often fall short. What works at low volumes may not hold up under greater complexity, size or energy demand. As the process scales up, gaps in containment, inadequate fire prevention measures or insufficient emergency-shutdown systems may arise
• Lack of process safety expertise. Many startups and scale-ups in TRL 5–6 do not yet have dedicated process safety experts on staff. Without proper expertise, it’s easy to overlook potential hazards, such as pressure-system failures or reaction runaways. This lack of expertise may also result in poor hazard analysis or inadequate risk assessments.
• Unclear or incomplete documentation. As processes become more complex, maintaining comprehensive documentation becomes a significant task. At earlier TRLs, informal approaches to documentation might suffice, but at TRL 5–6, the need for precise and thorough record-keeping becomes critical. Inadequate documentation of risk assessments, safety procedures and equipment specifications can lead to confusion, regulatory non-compliance and difficulties in training staff effectively.
• Scaling up without sufficient regulatory knowledge. As operations scale, the regulatory landscape becomes more complicated. Some regulations may not have been relevant at earlier stages, but they become mandatory as the process grows. Failing to identify and comply with industry-specific regulations can result in fines, delays and safety hazards. This lack of awareness often stems from not fully understanding the broader regulatory framework at this stage.
• Underestimating the complexity of new hazards. Scaling up often introduces new, previously unconsidered risks. The complexity of multi-step or continuous processes can create new hazards that are not immediately obvious. If these new hazards aren’t identified and addressed early, the result could be catastrophic — such as a reaction runaway, pressure-system failure, or chemical leak. Identifying and mitigating these hazards requires a proactive, thorough risk assessment.
By understanding these common challenges and why they occur, developers can take proactive steps to address them. Ensuring the right expertise, documentation, regulatory compliance and safety measures are in place will help mitigate risks and keep safety-scaling efforts on track.
Managing safety risks at TRL 5–6.
• Conduct a preliminary hazard and operability (HAZOP) study or a formal process hazard review. Before scaling up, it is crucial to assess process hazards early. If in-house safety expertise is limited, bring in consultants familiar with startups to help facilitate these reviews and set the groundwork for future scaling.
• Implement pressure-relief systems and fail-safe interlocks where possible. Ensure that all pressure systems have proper relief mechanisms and consider fail-safe interlocks that will automatically shut down processes in case of abnormal operating conditions.
• Review compliance status. Revisit the regulatory assessment conducted at TRL 3–4 to ensure that the organization is fully aware of all applicable regulations, understands the necessary actions and can demonstrate compliance.
• Update fire risk assessments. If inventories of flammable chemicals or materials need to be scaled up, conduct a thorough fire-risk assessment to identify potential hazards and ensure that adequate fire protection systems are in place.
• Monitor emissions and effluents where possible. Where relevant, begin monitoring emissions or effluents to identify potential environmental impacts, and ensure compliance with air, water or waste regulations.
• Formalize staff training in process safety. Start formalizing training for your team on process safety basics, emergency procedures and how to identify and report hazards as your systems scale.
TRL 7–8: Pilot production
This is often the most critical stage for safety, because processes become more complex and the potential for major accidents increases. At TRL 7–8, there is a transition from a small- to medium-scale prototype to a system that closely resembles commercial and industrial operations (Figure 5). The integration of continuous processes, utility systems and full operator involvement introduces new safety risks.
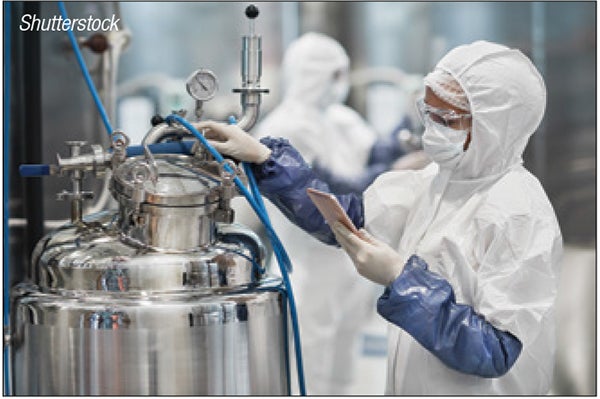
FIGURE 5. Pilot-scale systems resemble commercial operations, and the safety risks move beyond the immediate working environment
With the transition to pilot production, safety risks become more substantial, and escalation beyond the working environment must also be considered carefully.
• Loss of containment. As the scale of the operation increases, the risk of leaks, spills or gas releases escalates.
• Reaction runaways. Larger reaction vessels or systems introduce greater energy, which, if uncontrolled, can lead to dangerous runaway reactions.
• Utility failure impacts. The reliance on utilities (for example, power, water and cooling) means that a failure in these systems can cause widespread disruption or hazard escalation.
Common challenges (and why they happen). As the process moves into pilot production and demonstration at TRL 7–8, several challenges arise, due to the integration of new systems, the scaling of processes and the involvement of more personnel. Understanding the root causes of these challenges can help organizations take proactive steps to mitigate risks and ensure a smooth transition toward commercial deployment.
• Transitioning to full-scale operations without sufficient risk assessment. As the process moves from small-scale tests to pilot production, there is often a rush to scale up operations, which can lead to gaps in hazard identification and risk assessment. Without a thorough HAZOP study or process hazard review, potential risks, like reaction runaways or loss of containment, may go unnoticed until they escalate.
• Underestimating the complexity of utility systems. With the scaleup, the integration of utility systems, such as cooling, water supply or power distribution, becomes more complex. Startups and scaleups may not have the necessary infrastructure or expertise to manage these systems safely. Failures in these critical systems, such as power outages or pressure-system malfunctions, can have cascading effects on the entire operation. Failure to implement safeguards can result in accidents, downtime or non-compliance.
• Inadequate emergency-response planning. At earlier TRLs, emergency-response plans may have been basic or focused solely on laboratory-level accidents. As the scale increases, more comprehensive, site-wide emergency-response procedures are required, but they can be overlooked. If the team has not coordinated with local fire and rescue services or hasn’t conducted full emergency-response drills, there may be delays in responding to major incidents like chemical spills, fires or gas leaks.
• Limited staff training in process safety and emergency protocols. With the transition to a more complex operation, companies sometimes fail to provide sufficient training for staff. Employees may not be fully prepared for the risks they face, which can lead to human error, miscommunication and accidents. Training programs should evolve alongside process development to ensure competency.
• Increased pressure on documentation and compliance. As processes scale up, documentation and regulatory-compliance requirements become more stringent. What was previously handled informally or on a smaller scale now requires robust, traceable records. Failing to properly document risk assessments, design changes and safety procedures can result in non-compliance, regulatory audits and even legal action.
• Unforeseen technical and operational issues. Pilot operations often expose flaws in system integration, unforeseen technical challenges and operational inefficiencies that were not apparent in laboratory tests. Problems such as equipment failure, scaling issues or reaction instability may arise unexpectedly during pilot runs. These challenges require quick adaptation and often necessitate equipment redesigns, increased testing or process adjustments that need to be managed safely.
Proactively conducting HAZOP studies, establishing robust emergency-response plans and prioritizing staff training will help mitigate these risks and ensure a smoother progression toward commercial-scale production.
Managing safety risks at TRL 7–8.
• Perform a full HAZOP study. Conduct a thorough HAZOP study with an experienced facilitator to systematically assess risks and ensure that safety concerns are addressed before moving forward.
• Review your compliance status again. Revisit the regulatory assessment conducted at TRL 4–5 to ensure that you understand the regulatory implications of process scaleup, and understand the necessary actions required to maintain compliance
• Develop a management of change (MoC) procedure. Implement a formal procedure for managing changes in process, equipment or operating conditions. This ensures that safety is continuously evaluated when modifications are made.
• Establish basic layers of protection. Put in place foundational safety measures, such as alarms, interlocks and emergency shutdown systems. These layers are critical in preventing accidents or mitigating their impact.
• Ensure competent persons design, operate and maintain pressure systems. Under the Pressure Systems Safety Regulations (PSSR; www.hse.gov.uk), make sure qualified and competent personnel are responsible for designing, operating and maintaining any pressurized systems.
• Coordinate with local fire and rescue services. Work with local emergency services to ensure the emergency plan in place for the process is robust, and that the local first responders are familiar with the operations. This is especially important if an organization is scaling processes that involve hazardous materials or significant risks.
TRL 9: Commercial deployment
At TRL 9, a technology is ready for full-scale production. This is the point where safety management evolves from being project-specific to becoming an organizational responsibility, and safety management must be integral to daily operations, as the process technology is under the scrutiny of more stringent regulations, and non-compliance can have serious consequences. If a process involves hazardous materials that exceed certain thresholds, a technology may have major accident hazard potential and may need to comply with specific laws that govern this classification.
As you transition into commercial deployment, several key safety components become critical to ensure long-term success:
• Process safety management (PSM). PSM is a structured approach to managing the safety of a process throughout its lifecycle, ensuring consistent risk mitigation.
• Competency frameworks: Establishing clear competencies for roles involved in safety-critical operations, ensuring the team is qualified to manage complex hazards.
• Environmental permitting: Navigating environmental regulations to ensure compliance with emissions, waste disposal and other sustainability-related matters.
Common challenges (and why they happen).
• Maintaining consistent safety standards across a growing operation. As the process transitions into full-scale commercial production, the volume and complexity of operations increase, making it harder to maintain uniform safety standards across the organization. Inconsistent safety practices can arise as new production lines are added, or as more staff are hired to support operations. If safety standards are not enforced consistently across all shifts and departments, it increases the risk of accidents and non-compliance.
• Scaling up process safety management (PSM) systems. At this stage, PSM systems that were adequate during earlier TRLs may no longer be sufficient for the complexities of large-scale operations. The challenge lies in adapting and scaling these systems as your operations expand. Failing to formalize PSM processes or integrating them across all departments can result in gaps in risk management, leading to potential process failures, hazardous events, or regulatory violations.
• Compliance with evolving regulations. As the operation moves from small-scale to full-scale commercial production, the regulatory landscape can change. Keeping up with evolving regulations and ensuring ongoing compliance can become overwhelming. It is essential to have a clear understanding of the regulations that apply to your operations and develop processes for continual compliance.
• Ensuring competency across the organization. As production scales up, ensuring competency across a larger team can be difficult. Staff members with varying levels of experience and expertise may struggle to maintain the high safety standards required at this stage. A lack of competency in safety-critical roles can lead to incorrect decision-making, mishandling of hazardous materials, or failure to properly respond to emergencies. Ensuring proper training and certification for these roles is essential to maintaining a safe environment.
• Integration of environmental management and sustainability practices. With larger-scale production, environmental impact may grow, and regulatory scrutiny increases. At TRL 9, it becomes necessary to integrate robust environmental management practices into the operations. Failing to manage emissions, waste disposal and resource use efficiently can result in regulatory breaches or reputational damage. Environmental permits must be meticulously managed, and sustainability practices must be integrated into every aspect of the operation.
• Managing post-commissioning risks and incidents. Once the technology is commercialized, it may continue to evolve and require updates or adjustments to process equipment, safety systems or emergency response plans. This post-commissioning phase is critical to ensure the technology operates safely and efficiently in a real-world, high-volume environments. Without rigorous post-commissioning reviews, there is the risk that hidden hazards or system flaws emerge after full-scale deployment. These issues, if not addressed immediately, can escalate into serious incidents, impacting both safety and production continuity.
Understanding these challenges and their causes allows effective management of risks as the process moves into full-scale production. Ensuring consistent safety practices, maintaining robust PSM systems, staying ahead of regulatory requirements and prioritizing staff competency will help an organization navigate the complexities of TRL 9 and keep operations safe and compliant.
Managing safety risks at TRL 9.
• Formalize the safety management system. Align your safety-management framework with established standards, such as ISO 45001 and ISO 14001. A formalized system helps ensure that safety is integrated across all levels of the organization.
• Establish competency requirements. Clearly define the competencies required for safety-critical roles, and ensure staff are continuously trained. Maintain comprehensive records to demonstrate compliance.
• Perform safety integrity level (SIL) or LOPA assessments (in addition to HAZOPs). Conduct safety integrity level (SIL) or layers of protection analysis (LOPA), where relevant, to assess the reliability of process-safety safeguards, ensuring they are both appropriate and functional at scale.
• Maintain detailed records. Keep meticulous records of audits, inspections and incident investigations to ensure that safety practices are documented and auditable.
Concluding remarks
Across all TRLs, there are certain safety elements that remain foundational to success:
Competency. Everyone involved must be properly trained and supervised. Ongoing education and awareness are essential.
Documentation. Maintain detailed records of decisions, risk assessments and implemented safety controls. Documentation provides transparency for audits and compliance.
Ethics and reputation. Robust safety management is not just about rule compliance — it enhances a reputation, attracts investors and protects your team. Ethical safety practices contribute to long-term business sustainability.
Regulator engagement. If uncertain about regulatory obligations, contact the appropriate regulatory body early. Their guidance can help clarify requirements and prevent future compliance issues.
Safety isn’t a “tick-box” exercise — it’s a critical enabler of innovation. By managing it proactively and evolving your approach as technology scales, you reduce risk, protect your team and build trust with investors, partners and regulators.
To support your organization’s journey, draw on the wealth of guidance available — such as from the Health and Safety Executive (HSE) in the U.K., or a local equivalent. Engage early, leverage expertise and make safety a cornerstone of your success. While regulatory bodies provide essential resources, you can go further by involving experienced safety professionals — especially those familiar with the challenges of early-stage operations and the complexities of scaling hazardous technologies. With the right support, your organization’s approach to safety and risk management can become a strategic asset that propels innovations from breakthrough to impact.
Edited by Scott Jenkins
Author
Ngozi Chinye is a chartered chemical engineer and safety specialist with experience in process safety, hazard identification, HAZOP facilitation and risk management across the energy and industrial sectors. She has led and advised on complex safety studies for both established operators and early-stage technology developers, with a focus on embedding robust safety practices throughout the lifecycle of new processes. Chinye founded Soter Safety Consulting ([email protected]) to help startups and scale-ups navigate regulatory requirements, manage technical risk and accelerate innovation safely and responsibly. She is also the driving force behind HAZOP Edge®, a purpose-built software application designed to streamline HAZOP studies. Chinye is also a strong advocate for women in STEM.