New user-friendly solutions help chemical processors tackle tasks beyond design and optimization
Initially, steady-state simulation was used in the chemical process industries (CPI) to design a plant or a process. Advances in the technology, along with the need to produce more product in a more efficient and profitable manner, kick started the trend of using simulation tools to optimize new and existing processes. Today’s dynamic modeling, digitalization, more powerful computers and swifter calculation capabilities have led to increasingly prolific use of software by engineers in all facets of the chemical facility. Simulation software is now readily available to help with specific tasks, such as improving safety, operator training, increasing reliability and achieving corporate goals, including sustainability, energy efficiency and, of course, profitability.
Software advances
While steadystate simulators have been around for nearly 50 years and are still the go-to tool for designing and optimizing new processes or plants, the introduction of dynamic simulation has led to a wider berth of applications. “While steady-state simulators are doing a good job, dynamic simulators are the way to go for improving existing processes or checking the operability of a new plant,” says Marina Velazquez, senior product manager with Aveva Group plc (Cambridge, England; www.aveva.com). “Steady state is typically used early in the design to calculate sizing parameters and it assumes that the finished plant, equipment size and piping are exactly as they were designed. However, by startup, the location or size of the equipment and final piping may not be exactly as expected by the steady-state simulator. A dynamic simulator accommodates these differences and can be used to determine whether the control scheme is adequate, equipment will perform as expected, interlocks for safety are properly designed and more.”
Meanwhile, digitalization is further expanding the use of simulation. The “digital twin” is an exact replica of the physical plant, not as designed, but as it actually exists. It also incorporates live process and operating information from the operating plant. “The digital twin provides an accurate representation that is always ‘alive,’” says Rebecca Elgebrandt, portfolio marketing lead for Aveva’s engineering business. “Since the digital twin incorporates differences between the design of the plant and the actual plant, it moves the simulation needs from steady state to dynamic and provides the current status of the true assets, allowing users to run a simulation with ‘what if’ scenarios in an accurate twin of the plant before taking any actions.”
Roger-Marc Nicoud, CEO of Ypso-Facto (Nancy, France; www.ypsofacto.com) agrees that digitalization is an important step in simulation. “With a virtual/digital representation of a given process, one can easily experiment, test, train and explore operating conditions without the time and cost induced by real-life experimentation and without endangering real-life production.”
In addition, digitalization allows easy sharing of information between multiple engineering disciplines. “Operating processes and facilities requires the joint expertise of molecule specialists and simulation experts, of industry engineers and scientists and others, all with the single shared goal of inventing the best possible processes in an unbiased manner,” says Nicoud. “And, today’s simulation tools aim to bring all the necessary actors together and facilitate collaboration.”
Velazquez agrees that information sharing is a growing necessity. “Integration is becoming more important so that all the process data can be shared among all the engineering disciplines,” she says. “The final design, sometimes completed two or three years after the first simulation was done, can be checked easily by the dynamic simulation before starting up, reducing and avoiding costly last-minute updates at startup. Chemical processes can benefit from checking operating and control schemes prior to startup and from other simulation activities such as operator training, and digitalization allows better integration to make the necessary information sharing and collaboration easier for all the disciplines involved in these steps,” she says (Figure 1).
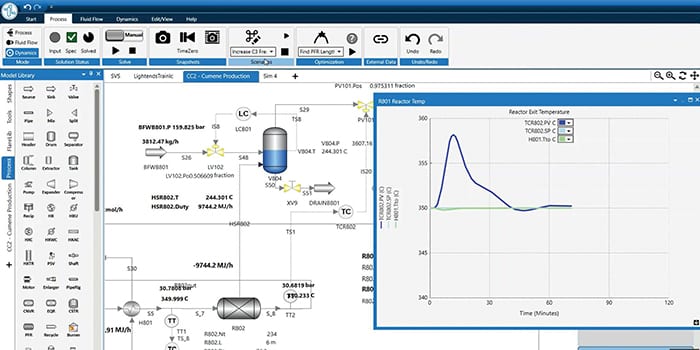
Figure 1. The SimCentral Simulation Platform from Aveva can improve the workflow, safety and design of a chemical process
Aveva
Increased speed and improved user friendliness are also moving simulation into more applications. “While many simulation solutions are perceived as being very accurate, often the other perception is that they are time-consuming and take a lot of experience to use,” says Ahmad Haidari, global industry director, process, energy and power, with Ansys (Canonsburg, Pa.; www.ansys.com). “However, newer versions don’t require the same amount of experience and hands-on time as prior versions, which makes simulations more accessible and much more routine in the chemical processing industry.”
For example, Ansys is focused on task-based workflow, which presents only the features and choices relevant to the task at hand and has best practices built in. “This provides the ability to use defaults and still get good answers, and also to customize and build workflows so that other engineers with less simulation experience can duplicate results. We are finding that this allows engineers to accomplish simulations two to three times faster than in the past with significantly less training,” explains Haidari.
The company is also working to improve meshing. “One area that has been frustrating with fluid-dynamic-based solutions has been the meshing process, because in order to get a good mesh for use with simulations, a certain amount of hand-repetitive tasks were necessary to fine tune that mesh,” he explains. “We are automating that process through a new technology to virtually eliminate the hands-on piece. Things that took two to three weeks to prepare are now getting done in hours. Engineers who are really experienced in chemical engineering, but don’t have experience with fluid dynamics will be very successful using these tools,” he says (Figure 2).
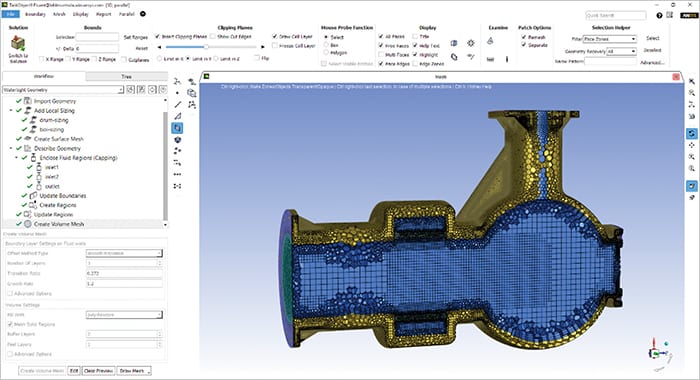
Figure 2. Ansys Fluent’s Mosiac-enabled task-based workflow meshes complex geometries twice as fast with minimal user inputs
Ansys
Another example is Chemstations (Houston; www.chemstations.com), which is launching a new version of its first-principles-based simulation software with improved calculation speeds that come via parallel processing that uses all available computing cores. “This means that instead of using just one core of the user’s computer, we can spread the workload across as many cores as are available, which will speed the process considerably,” explains Steve Brown, president of Chemstations. While the initial intent of the improved calculation time was to allow faster execution of large optimization projects, Brown says the increased speed also allows the software to be used for smaller projects. Wendy Young, marketing manager with Chemstations, agrees: “In the past, scaled-down versions of optimization, such as a sensitivity study, would take too long, but the calculation time has been reduced to such a degree that engineers are more likely to run simulations for smaller studies.”
A wider berth of applications
While simulation tools used to be firmly rooted in design and optimization of plant and processes, digitalization, easier collaboration and user friendliness have opened the door for the use of simulation throughout the plant.
Plant safety. “The evolution of computational power and the capabilities of the software have given engineers a chance to solve some different, even possibly more complex, problems, with a higher degree of confidence,” says Haidari with Ansys. “Safety is one of the areas where simulation is now being applied to determine why or when leaks, corrosion or other factors that deteriorate performance and directly impact safety of the process and personnel are happening.”
For example, leaks may occur due to deteriorating seals or erosion of equipment, but because advanced tools allow users to model seals or examine corrosion in a given operation, the potential for failure can be determined. If there is a leak, simulation can be used to look at how gas may be dispersed within the plant using all sorts of possible scenarios, including wind and location of stacks. Safety valves can be better designed via simulation tools, and advanced software allows users to simulate what happens when an explosion occurs so they can better design equipment and plan for an emergency.
Paige Marie Morse, chemicals industry marketing director, with AspenTech (Bedford, Mass; www.aspentech.com), agrees that simulation tools can be helpful in the area of plant safety. For example, the company has acquired Blowdown software technology, which is used to identify locations in a system where temperatures can decline dramatically during depressurization. Blowdown has been incorporated into Aspen Hysys in order to provide an accurate determination of these low temperatures, which is a critical activity in the design and operation of process plants as it can improve safety of the plant (Figure 3).
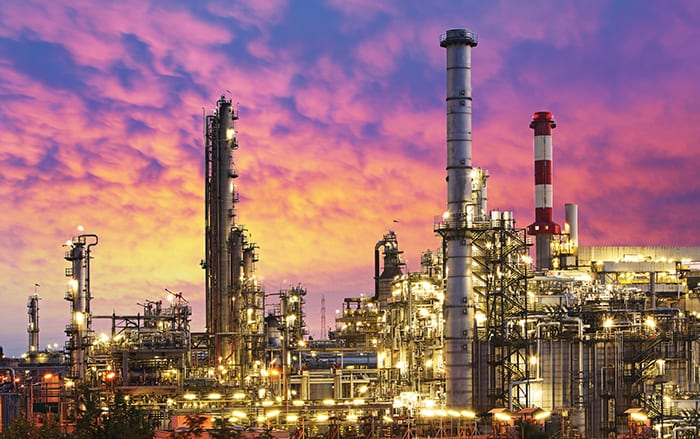
Figure 3. Simulation used throughout the entire plant asset lifecycle improves safety and other pillars of operational excellence
AspenTech
Simulators can also be used to avoid unnecessarily purchasing safety systems. “A digital twin environment can be used for testing levels of protection, as well as for reducing and evaluating capital investments for safety stewardship,” says Mart Berutti, vice president of process simulation with Emerson (St. Louis, Mo.; www.emerson.com). “The investment of capital in process safety is necessary and very important, but it’s not one that increases the production of the plant. Simulation can help processors evaluate what levels of safety protection are required and eliminate the systems that aren’t necessary.”
Reliability. Today’s simulators can also be used to enhance reliability of the plant and equipment, says Ansys’s Haidari. “We call this ‘fitness for service,’ which means we look at things like fouling or degradation that may impact the performance of equipment. It is possible, through simulation, to look at a given design, either before it is built or during operation, and examine the range of operating parameters and variables it will be exposed to and understand the life of that asset,” he says.
Further, he says it is possible to use simulators to look at issues that may be occurring, such as vibration, and use the model to perform a cause-and-effect analysis to understand why it may be vibrating and remedy the situation.
Training. Training is another area where simulators are making a major impact. “There’s a lot of interest in the use of simulation for operator training,” says AspenTech’s Morse. “The advantage of using a digital representation of the plant is that it allows you to, offline, take operator trainees through different scenarios. Because it is a digital twin, it reflects what is going on at the unit so operators can learn how to handle various tasks without making an impact on the actual plant. It can also be used to train new operators before a newly constructed plant is up and running.
“Additionally,” Morse continues, “Simulation can be used to create scenarios that involve process upsets, safety emergencies or environmental incidents and train operators to react so that events are properly managed and so operators have experienced the issues and don’t panic in a real-life incident.”
Emerson’s Berutti agrees that simulator training is a vital application. “Statistical information shows that it takes six to seven years for a chemical plant operator to be able to make good risk-based decisions concerning operation of the plant, but most facilities are not in a position to spend this amount of time getting operators up to speed,” he says. “A digital plant environment provides us with a time machine. It allows new operators to get comfortable with running the plant and controls for daily operations without actually practicing in the real plant. And, operators can have experiences — upsets and failures — that we would never want to see, but if they happen, the operators have had the opportunity to experience them over and over in the digital twin. This allows them to think clearly and not be intimidated by the gravity of a situation and have the competency to handle it. It makes them ready to operate the plant and deal with emergencies in a shorter period of time.”
Corporate goals. Modern simulation tools can also help processors achieve corporate goals, including energy efficiency, sustainability and profitability. “Simulation was created for the purpose of increasing efficiencies, so it makes sense that it is used for corporate goals such as sustainability and energy efficiency,” says Stephane Dechelotte, CEO at ProSim (Labege, France; www.prosim.net). “Advances in software, such as better thermodynamic models and those specifically designed to assist with energy evaluations, allow better simulations of energy estimation and profitability calculations. Today’s users require models that are predictive and that cover a wide range of mixtures, temperatures and pressure conditions, so thermodynamic models are a critical component to running simulations that achieve corporate goals, such as energy efficiency and the impact it has on yield, he says” (Figure 4).
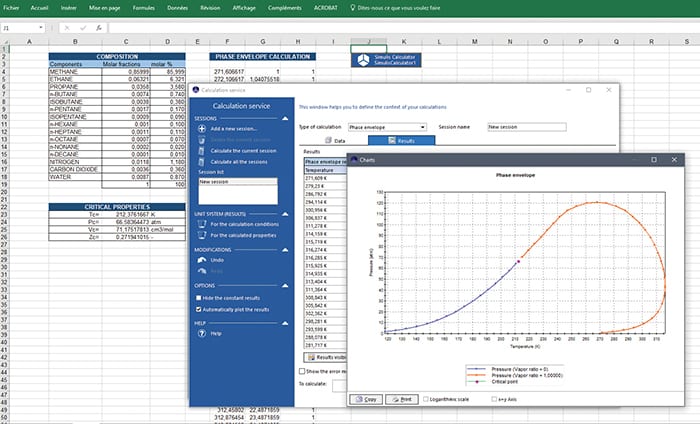
Figure 4. ProSim’s Simulis Thermodynamics provides the thermodynamics knowledge needed for chemical process simulation. It is available as a Microsoft Excel add-in, a toolbox in MatLab or as a software component that can be plugged into any other application/software requiring reliable and accurate thermophysical properties. The figure shows a phase-envelope calculation diagram
ProSim
Chemstations’s Brown agrees that simulation is finding greater application in this area. “Companies will do an analysis to see where they can boost profitability and this is almost always tied to energy consumption. However, the same company may also consider energy efficiency a corporate social goal,” he says. “We’ve seen them use simulation to perform a multi-objective optimization where they have the first objective as profit and the second as the societal or environmental impact. They can use the simulation to look at how they may want to operate the facility and examine the results and decide, on a corporate level, with input from various engineering disciplines, where to balance profitability with social or environmental impacts. They can find the overall optimum that works for their company.”
These same types of simulations can be applied to almost any corporate goal, says Ansys’s Haidari. “The process industry is becoming very interested in sustainability and as such,is looking at things like resource scarcity, emissions reduction and pollution control, shifting to a low-carbon economy and other social aspects of processing,” he says. “Today’s easier-to-use and advanced simulations allow processors to perform studies around sustainability goals such as waste treatment, improving reactions to reduce the amount of heat created, taking wasted resources and putting them back into the process, reducing emissions, improving energy performance and reducing or recycling water or other resources used in the process.”
What it comes down to is that today’s simulators are capable of doing more than those of the past and they are able to do it dynamically and digitally, while sharing accurate and up-to-date information with everyone in the plant who might need it. “Safety issues, energy issues, control issues, reliability issues…all these issues can be solved if the engineers can communicate amongst themselves in the same language and that language is simulation,” states Chemstations’s Brown.