An intelligent approach to developing the scope of retrofit projects can allow facilities to remain competitive in the marketplace and meet regulatory requirements
Timely and well executed retrofit projects are critical for most facilities in the chemical process industries (CPI) as they strive to remain competitive players in the marketplace, meet the owner’s business needs and maintain regulatory compliance. Retrofit projects and new-facility projects lie on a spectrum, with the two having many similar requirements and qualities (Figure 1). With a sustainable plan and schedule, retrofit projects can be accomplished incrementally. The benefit of this approach is an “evergreen” facility that is responsive to business needs. This article focuses on scope development for revamp and retrofit projects, and presents many of the important considerations for undertaking a retrofit project.
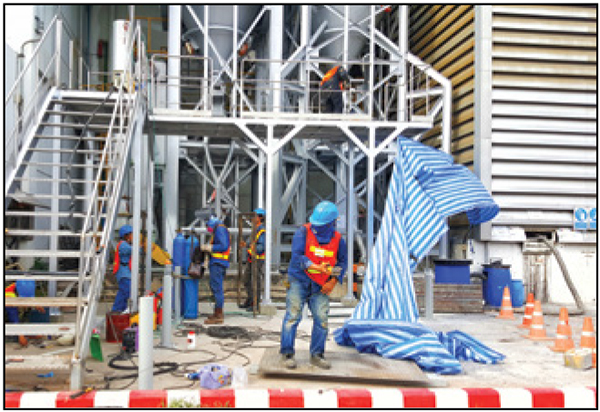
FIGURE 1. It is often the case that making improvements to CPI facilities is more cost-effective than replacing them
Retrofit versus revamp
A “revamp project” replaces or upgrades equipment or systems to increase production capability or performance in an existing facility or industrial site. A “retrofit project” modifies, enhances, debottlenecks, or otherwise improves an existing entity, rather than involving the creation of an entirely new entity. In contrast, a new or “greenfield” project involves building a new facility on a new site (a greenfield), and is unconstrained by existing facilities. For the purposes of this article, these project types (retrofits and revamps) are considered identical.
Cost-benefit considerations
There are many factors at play in determining the scope, as well as the costs and benefits for a retrofit project. The following are a set of questions that should be worked through as the retrofit project begins.
Does the retrofit involve a “replacement-in-kind” of equipment? In cases where capital equipment may need to be replaced, it is often useful to start with how long the equipment has been in service. Most capital equipment is expected to have a 20-year minimum service life. If equipment is being replaced before the expected service life, determine whether there is a deficiency in design, reliability, performance, controls or installation. Here are some possibilities to consider:
• The application might require a different type of equipment
•The required reliability might demand a different metallurgy or service factor
• The normal and peak operating requirements might exceed the equipment’s rating
• A more sophisticated control strategy might be required. For example, a pump with intermittent operations might require a discharge control valve, bypass line or variable-frequency drive to minimize pump starts and stops
• The equipment installation might put excessive mechanical or hydraulic stresses on the equipment or connections. For example, high temperatures can cause significant pipe expansion, which will require expansion joints, or a design that has adequate flexibility
• For critical equipment, the schedule might require a replacement-in-kind while a longer-term solution is developed and implemented
These are only some of the factors justifying an “upgrade” instead of a “replacement-in-kind”.
Is the retrofit an upgrade or enhancement project? If the equipment has been in service for a significant period, have there been technological improvements since the last installation? Improvements in equipment design, reliability, performance and efficiency are generally always occurring. For example, like automobiles and household appliances, industrial equipment has become automated, with significant benefits. Metallurgies have become more specialized, with alloys to reduce corrosion. Piping and electrical standards might have improved. The connecting pipe and electrical service might need to be upgraded.
Are safety or environmental performance upgrades required? Because they are already in operation, certain processes at CPI facilities are exempt from new standards (that is, they are “grandfathered” into meeting the requirements of the new standard). However, if it is part of a retrofit project, a process might require upgrades for safety, efficiency or environmental performance. For example, environmental and reliability requirements might require some rotating equipment to have sophisticated shaft-seal systems with barrier fluids.
Have equipment manufacturers consolidated, relocated, or gone out of business? Equipment considered “state of the art” twenty years ago, might not be available or might not meet current standards.
Will infrastructure changes be required? Improvements of new equipment might require an upgrade of the infrastructure (Figure 2). For example, automated equipment will need data connectivity. With different metallurgies and standards, the process and utility tie-in scope might need to include more pipe, electrical or controls scope. Different equipment designs might have different footprints, with different connections, support requirements and access points. If a process is being upgraded, the decisions become more complex. The scope might require the upgrade of a system with increased or different utility requirements.
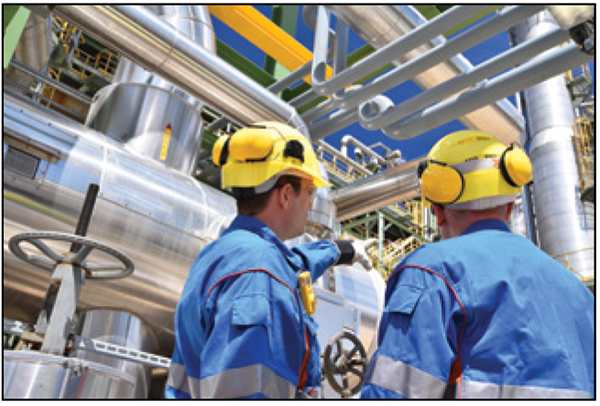
FIGURE 2. Improvements in equipment may require changes to the plant’s infrastructure
Is the retrofit project a capacity increase or a debottlenecking project? A “bottleneck” constrains or limits a process. Bottlenecks can be identified in the manufacturing process by reviewing operating data and by modeling the process. An example is a manual drum-loading step in a manufacturing process. If a capacity increase is expected, the entire process will need to be evaluated to confirm the capacity is feasible. Review the current process and facility drawings, equipment and building layouts, and hazardous area classification drawings.
Some examples of debottlenecking projects include the following: An automated bulk charging system can improve cycle times by reducing the process charging time. Installing a larger pump or heat exchanger may not provide a production increase if the process and utilities inputs and outputs do not meet the new equipment’s requirements. Keep in mind, though that higher flows might require larger pipe diameters to prevent high velocities (erosion) or high pressure drop (inefficiency). Also, heat exchangers are designed for certain fluid velocities for best heat transfer efficiency. As with piping, higher flows might require larger flow areas. Due to hydraulics and residence time, processing vessels and towers have certain high- and low-flow requirements for best operation.
Plan and scope development
The next phase of the retrofit project involves developing process flow diagrams, piping & instrumentation diagrams (P&IDs) and layout drawings of the retrofit options. “Redline” changes should be made to the existing facility design. These could include changes to piping connections for utilities, vents, drains and controls. Also note changes to valves for operation, isolation and bleeds. Consider access for construction, operations and maintenance.
The boundaries of a retrofit project need to be considered: In a retrofit project, the facility and supporting utilities are expected to be reused (with maybe selective upgrades). Otherwise, the project becomes a “new facility” project, not a retrofit. As an analogy using houses, a retrofit is “remodeling” not a “tear down” project. Installing more equipment in a fixed area will reduce operations and maintenance access. A larger footprint might encroach on setbacks from administrative areas and property lines. The existing facility will be reused, although the unit will likely be idled for the duration of the demolition (removal of replaced assets) and installation of new assets.
Design and execution planning
Planning is critical to any project’s success. Many of these requirements are identical to any medium- to large-sized project, whether a retrofit or new facility. The design of the new retrofit assets needs to be integrated into the operations and maintenance procedures. Otherwise, there is a risk of unintended issues and inefficiencies.
Consider the owner’s project resources. An owner has operating and maintenance staff with tasks and objectives assigned by management. Taking on project team responsibilities for a retrofit project will require a realignment of responsibilities. Engineering consultants can undertake the effort needed to support a retrofit project. However, the owner’s personnel will still need to support the consultant with operational knowledge and approve final decisions. The scope of new or reused infrastructure needs to be balanced with cost, schedule and performance.
In planning, plant engineers must be cognizant of the required design standards and codes. They should ask whether there are performance and efficiency requirements for new or reused utilities, and environmental systems. Also, there may be new or tie-ins to safety systems, such as new vents or relief valves, or tie-ins to exhaust systems. The operating environment and permitted operations should also be considered for potential hazards.
Normally, a process outage is required to dismantle and remove the existing equipment before installing the new equipment (Figure 3).
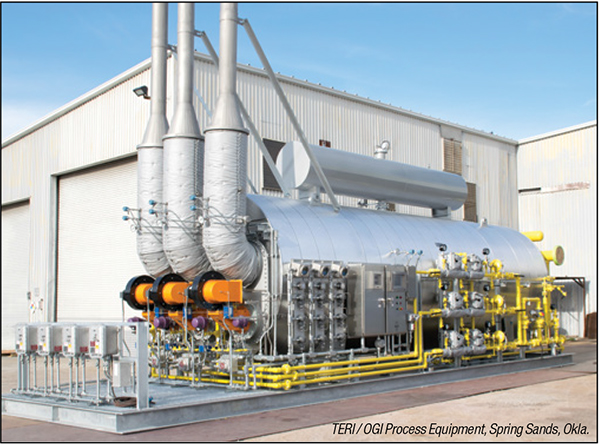
FIGURE 3. Process outages are required to install new equipment, such as the heater shown here
Projects may require changes to plant infrastructure, so the necessary tie-ins to piping, electrical and controls and utilities should be clear, as well as the need for potential new concrete and steel buildings for the storage and warehousing of raw materials or final product. There may be a need for new environmental systems.
Infrastructure requirements
If changes to plant infrastructure are required because of a retrofit project, there are several guidelines that should be followed.
• Consider access requirements for operations and maintenance staff. Instead of ladders, platforms might be needed, for example, especially if tools and equipment are required at the access point. Davits or overhead rails might be needed for removal of equipment
• Consider the impact of the infrastructure changes to owner’s and external stakeholders. Where there are impacts, contact the appropriate owner stakeholder and evaluate the current environmental permit limits. Also, consider the current zoning of the owner’s facility. Requirements waived due to grandfathering might be required for a retrofitted facility. If the amount of impervious surface is increased due to the infrastructure changes, then the stormwater runoff systems need to be evaluated
• Consider operator training and appropriate staffing levels (for startup and operations)
MoC and risk review
Whenever there are new processes being introduced or existing processes being revised, a management-of-change (MoC) approach should be used to systematically evaluate new and revised processes.
At major project milestones, safety and risk reviews should occur, particularly when making funding and permitting decisions.
Procurement
Planning is needed for the specifications, bidding and deliveries of critical equipment. The general best practice is to include the owner’s purchasing agents early in the project schedule. At this stage, master service agreements and terms and conditions for the project will need to be established.
When making bid award decisions, the technical capabilities of the vendor companies involved should be carefully considered along with the pricing. Vendor construction, startup and follow-up support capabilities should be taken into account.
When assembling a procurement plan, spare-parts inventories for new equipment should be a part of the process.
Determine what items are “specialties,” which would be purchased individually with specifications, and what items are treated as “bulk,” meaning they can be purchased by the construction contractor.
Construction and startup
Determine the schedule for project approval, design, procurement, construction and startup. Include outage planning also for retrofit projects. New facilities can be constructed in parallel (or remotely) to an operating facility.
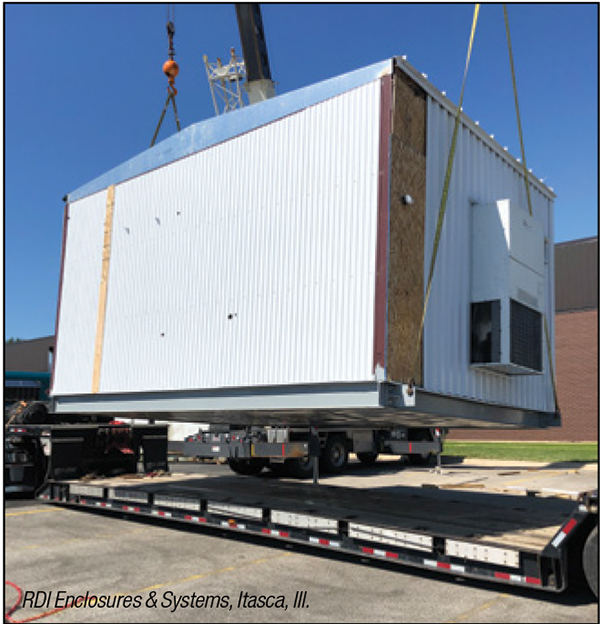
FIGURE 4. Prefabricated buildings, such as the control room shown here, may be prepared off-site and installed later
For the construction schedule, the following items should be considered:
• Appropriate level of off-site pre-work may be desirable, such as skid fabrication for equipment, pipe spools, prefabricated buildings and enclosures (Figure 4)
• Consider logistics (road permits and access to the site)
• Make piping tie-ins with valves at a more convenient time during a maintenance outage
• Make electrical tie-ins during maintenance outages. For example, install a motor starter or motor control center for project motors
Remember that the construction contractor’s personnel and equipment will need access to the facility for parking, administrative facilities and material laydown areas, as well as physical access for work
The level of fabrication and construction inspections is important. Normally inspections are performed by either the owner’s contractors or third-party contractors. There will be documentation requirements for the owner’s regulatory groups and permitting requirement for municipalities and agencies.
At the conclusion of the retrofit project construction, operations and maintenance personnel will be needed for checkout, and construction personnel are needed to resolve punch-list item resolution. In addition, vendor personnel will be needed for the startup of specialized equipment.
Edited by Scott Jenkins
Author
Alan McCurdy retired from Valdes Engineering Co. (100 22nd Street, Lombard, IL 60148; Email: alan.mccurdy54@gmail.com) in 2020, but remains active part-time in certain projects. He has 40 years of experience as a project manager of engineering projects in pertroleum refining, chemical manufacturing, natural gas utilities and industrial facility settings. As a senior project manager at Valdes, McCurdy sheparded engineering design projects from concept to design and procurement and construction to startup. McCurdy holds a B.S.Ch.E. from Carnegie Mellon University (1976) and an MBA from the University of Louisville (1985). McCurdy has extensive knowledge of procedures and tools used by his employers, clients and associates, as well as analytics and tools from his MBA courses and quality and statistics training. In addition, McCurdy was a member of the U.S. Army from 1976 to 1980.