Information provided here offers a basic primer on the features and functions of dryer types, with a focus on fluidized-bed dryers, for moisture control in industrial operations
The ability to control the moisture of solid materials while drying plays a critical role in the chemical process industries (CPI), including agriculture, chemicals, plastics, pharmaceuticals and others. Almost every plant that handles powders or granules requires a dryer of some type within the facility, and the challenge becomes which type of dryer will best suit a particular application and the specific material to be dried? This article is a basic primer on the features and functions of different dryer types, and aims to help in the selection of the right dryer for specific moisture-control applications.
The two overarching categories for dryer types are direct and indirect dryers. A direct dryer uses hot air as the mechanism of water evaporation. An indirect dryer uses rotating heat surfaces to transfer heat into the wet material.
Of these two types, the most common is the direct-style dryer, in which natural gas is used as the fuel to heat the air. However, no single dryer suits every application. An examination of the various features can help determine which type of direct dryer will best suit a given set of specifications.
Dryer design: ‘weather system’
A deeper understanding of the direct-drying process can be obtained by assuming the role of fluidized-bed “meteorologist” to model the air and moisture properties during various stages of the drying process. Figure 1 depicts the four stages of a direct-dryer system.
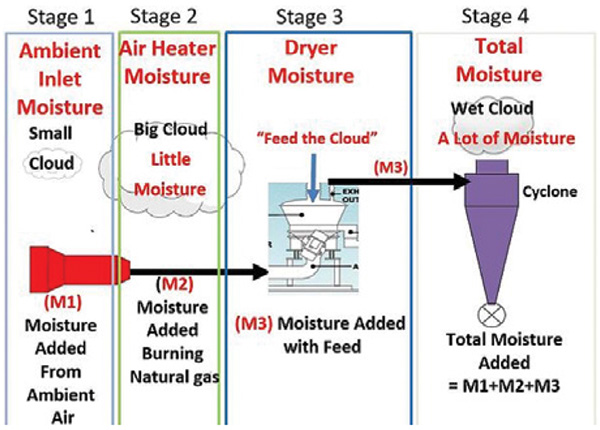
FIGURE 1. The four main stages for a direct-drying system are shown here
Each stage illustrates a cloud formation, with the shaded areas representing the relative amount of water vapor, the cloud’s expansion and absorption of water vapor during each of the four stages. A psychrometric chart helps model the process.
Stage 1 shows the inlet with the ambient moisture (amount of water vapor per unit of dry air) coming into the dryer. The cloud is small, reflecting the size and amount of water vapor present.
In Stage 2, the air is heated to the inlet air temperature. The greater the amount of heated air from the natural-gas air heater, the more the air expands, enabling it to carry away more water vapor. This may be perceived from the psychrometric graph as well. Heating the air increases its temperature and is depicted by a horizontal line in the graph. While the total water content remains unchanged, the ability of air to hold moisture significantly increases. In other words, the relative humidity decreases as we heat the air. Depending on the inlet air temperature, the specific volume of air may double. Some additional water vapor is added to the cloud by burning natural gas.
Stage 3 illustrates the screw feeder dumping moisture-containing solid product into the dryer, thereby “feeding” the cloud.
In Stage 4, the moist air is expelled from the machine as the cloud cools and contracts, while still retaining the water vapor from the prior stages. The relative percentage of moisture in the outlet air can be measured by its relative humidity, the percentage of actual vapor pressure divided by saturated vapor pressure, or the adiabatic saturation ratio (ASR), and the percentage of the actual weight of water vapor over the weight of saturated water vapor.
While some may be more familiar with the concept of relative humidity, this measurement is more commonly used with heating, ventilation and air conditioning (HVAC) systems and is not as applicable at much higher temperatures. On a psychometric chart, the ASR is mathematically split into ten equal percentages. The ASR tops out at 100%. This means that at 60% ASR, it is possible to add 40% more water vapor to reach saturation.
Depending on the temperature profile, most direct dryers will fall within an acceptable range of 70 to 90% ASR and be able to attain the desired final product moisture.
The challenge with a direct dryer is maximizing the time the wet feed is in contact with the heated drying air. A checklist of major factors that will affect drying rates, efficiencies and features will impact the selection of the proper direct-drying system. These factors can include:
- Air flowrate
- Air flow direction
- Moisture content of materials
- Heat sensitivity (maximum allowable temperature)
- Layout
- Backmixing (see Box 1, right)
- Agglomeration
- Particle range, size, color and shape
- Plant footprint
- Thermal features (other than drying)
- Sanitation
- Throughput
- Maintenance
- Special material considerations, such as explosive or combustible materials
Drying curve
Materials’ drying curves show the reduction in moisture over time as the material is processed (Figure 2). Flash dryers supply a swift initial moisture reduction; however, they are not always the most effective in obtaining the lowest moisture content.
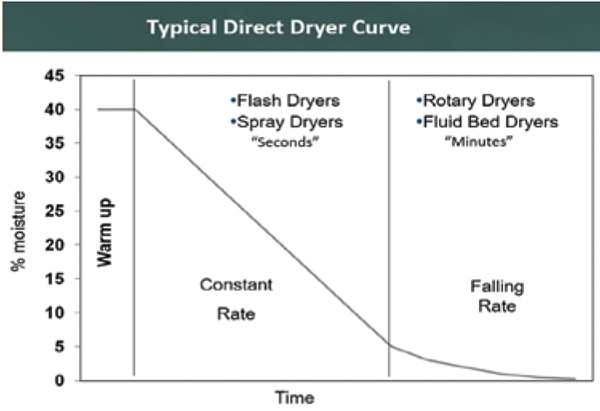
FIGURE 2. Flash dryers supply a rapid initial reduction in moisture content, but reaching lower moisture levels requires longer residence time
Reaching lower product moisture levels overall requires a longer exposure time to allow moisture to migrate out from the particle’s center. For that reason, dryers with a longer residence time, such as a rotary, conveyor or fluidized-bed dryer, will give a more consistent, low-moisture-content result.
Solids processors might select a two-stage system that takes advantage of the complementary benefits of two different types of dryers; the short heat exposure of a flash dryer, followed by a longer term of exposure in a secondary dryer
Temperature and testing
Ultimately, the only way to know precisely how a dryer will perform with a particular material is to perform testing. Typically, manufacturers will have a small laboratory test dryer, where it is possible to run small batches at different drying times and temperatures. After conducting tests in smaller dryers, the scale-up calculations take into account the retention time (determined by the volume of the bed and the flowrate of the solid material) to determine the heat and mass balance needed to scale to a larger dryer.
Heat loss of each dryer is individual, depending on the size and insulation of the dryer. For example, smaller dryers have a higher range of heat loss due to larger surface areas compared to airflow, amounting to up to 20% more heat loss compared to larger dryers. One of the advantages of relatively short retention direct dryers is the evaporative cooling effect as the feed material dries. For that reason, the “rule of thumb” of the inlet air temperature can be as much as 50ºC above the sticking point or degradation point of the material. The outlet air temperature (the temperature of the vented air after drying) is vital in controlling the product moisture. Some dryer operators control the wet-bulb or the dewpoint temperature to control product moisture. The temperature and water-vapor loading of the outlet air stream will relate to the final product moisture.
Dryer types
Brief descriptions of various types of dryers used in industrial drying applications follow.
Rotary dryers. Rotary dryers are designed with rotating, tumbling drums and internal lifters that cause the moist solid to “rain” down through the passing and heated drying air. The challenge related to this dryer is maximizing the time the wet feed is exposed to the heated drying air: the better the contact, the shorter the rotary dryer’s length and the lower the cost. Final design will depend on the retention time required.
Conveyor belt dryers. Conveyor dryers (also called belt, tunnel or apron dryers) are rotating belt conveyors typically equipped with a perforated belt to allow heated air to circulate through the belt and the wet feed. The challenge for this dryer is getting the heated air into contact with the inner layer of the feed on the belt. Some use multiple belts to reorient the feed and expose internal surfaces to the heated air.
Spray dryers. A spray dryer begins with a liquid feed or slurry, progresses to atomization of the liquid or converts it into smaller droplets. The goal is rapid drying of liquid material into a powdered material using heated gas. Many different types of spray dryers are available and commonly used within the food, chemical and pharmaceutical industries. Spray dryers often will be used in conjunction with a fluidized-bed dryer, as complementary systems to achieve the target moisture level.
Flash dryers. A flash dryer is a hot pneumatic conveyor. The challenge is to increase the exposure time from a few seconds. There are variations, such as recycling large particles or inline particle size reduction to aid in drying. Flash dryers are used in processing food or minerals that may be sensitive to prolonged heat exposure.
Fluidized-bed dryers
Fluidized-bed dryers use heated air to fluidize and dry feed material and are either static or vibrating in design. Static fluidized beds can have bed depths that minimize the size of the dryer and the amount of drying air required. The inefficiency of a direct dryer is the exhausted hot air; minimizing the amount of air increases the dryer’s efficiency.
Fluidized-bed dryers come in two different shapes: rectangular or circular. Fluidized-bed dryers (and coolers) offer batch and continuous processing capabilities.
Rectangular versus circular fluid-bed dryers. A rectangular fluidized-bed dryer operates on a conveyor-style movement for material transport through the dryer. These can be built to higher capacities and with multiple stages. Rectangular fluidized-bed dryers offer a viable option for a high-volume, continuous application that does not require stringent adherence to rigid sanitation standards. However, the larger size requires a substantial plant footprint and can be a challenge to install, clean and maintain, with the largest sizes requiring a crane or forklift to maneuver.
One of the challenges for a rectangular fluidized-bed dryer is the “dead” areas in the dryer’s corners that can trap or retain previously processed materials or harbor bacterial growth. In case of product or material retention, the material with a longer dwell time can overdry some materials. In food, pharmaceutical and similar applications, fast and thorough cleaning capabilities are critical to comply with 3-A, USDA, FDA, BISCC and other stringent sanitary and safety standards.
Circular fluidized-bed dryers offer both batch and continuous drying capabilities, with batch offering greater operator control of the final moisture level. In applications where the specifications are not as tight for final moisture levels or if they fall within a range, the operator can opt for a continuous drying process.
The circular design is free from internal corners or edges, offering easier maintenance and cleaning options than a rectangular version. A circular fluidized-bed dryer can often complete a cleaning cycle in an hour or less, while a rectangular fluid bed can take up to an entire shift.
Materials processed in a circular vibratory fluid bed move in a spiral motion, providing even airflow and vibration throughout the bed to separate and fluidize individual particles. This motion maximizes material surface area and drying, with the materials entering and exiting cleanly. This supplies a more homogeneous moisture level from batch to batch. The design allows for precise control of air temperature and airflow, bed depth, dwell time and material flow paths.
The design of the circular models offers an inherent strength to the operator ancillary benefits. Construction materials can be downgauged, vibratory motors downsized for quieter operations and associated components eliminated for a lighter machine. Of particular note, energy savings are significant, consuming 20 to 50% less power on average than a rectangular model when comparing similar throughput and while achieving similar moisture content.
Plant footprint is greatly reduced compared to a rectangular fluidized bed as well, which is significant when evaluating throughput per square foot of factory floor space (see Box, right).
A vibrating fluidized-bed dryer can handle a much wider range of shapes, sizes and densities in addition to friable materials. This includes products within industrial manufacturing areas as diverse as the following:
- Wood flour
- Agricultural chemicals
- Fertilizers
- Catalysts
- Agglomerates
- Ceramic beads
- PVC powder
- Sodium maleate hybrid and similar materials
- Recycled plastics and glass
Concluding remarks
Industrial direct-dryer design takes into account a multitude of factors, and no single dryer a perfect fit for all applications. Educate yourself about different dryer functions and features when seeking the right equipment for your specific drying applications. Research available dryer types and be sure to analyze the conditions at any point of the four stages of drying to obtain the best understanding of a direct dryer. Pay particular attention to the temperature profile, retention time, airflow and moisture reduction capacity, as well as customization options for more unique drying situations. Most importantly, make sure to test your material on any style dryer being considered before getting an estimate. Vendors should be willing to accommodate this step in the dryer-evaluation process.
Edited by Scott Jenkins
Author
Lance Briggs is the vice president of sales and business development at Kason Corp. (67 East Willow St., Millburn, N.J. 07041; Phone: 973-467-8140; www.kason.com). Briggs has a keen interest in bringing creative solutions to diverse customer challenges. He has a strong background of providing solutions and process implementation to customers. Briggs began his career as a product engineer and manager before moving to technical sales. He now leads commercial efforts for North America for Kason Advanced Materials Processing division. His degree is in mechanical and aerospace engineering from the University of Missouri.