Continuous flow measurement is used at this Austrian specialty chemicals manufacturer for process optimization, as well as overload protection
Sensing-plate weighing systems are often used for weighing free-flowing and very dusty bulk materials. Such solids flowmeters ensure reliable determination of material throughput rates, even in harsh environments. An Austrian specialty chemicals manufacturer uses continuous-flow measurement for process optimization of its additive production, as well as for overload protection of separating sieves — over a wide measurement range.
Background
Additives are auxiliary substances or supplements and contribute significantly to improving the properties of the main product, either during production, storage and processing or in subsequent application. For most additives, the rule is: minimum use, maximum effect. They are always optimized for special applications, and are often custom-made. This results in rather low production volumes and a very high effort in research and development.
Tribotecc GmbH (Arnoldstein, Austria; www.tribotecc.com), a member of the Treibacher Group, is the world’s leading manufacturer of metal sulfides. As functional additives, metal sulfides are used in brake and clutch linings, as well as in lubricants and abrasives. More than a dozen natural and special synthetic metal sulfides are available. At the specialty chemicals company, therefore, everything revolves around friction. The science of friction (tribology) explores the relationships between friction, wear and lubrication.
These relationships are of immense importance for our everyday lives, as well as for the economy — they determine the wear of machines, as well as energy consumption and thus CO 2 emissions. Around the world, Tribotecc’s innovative products help ensure, for example, that engines consume less, gearboxes last longer or bearings are practically maintenance-free due to synthetic solid lubricants.
Key to quality
Consistent product quality is crucial to the success of the company. The manufacture of the precisely specified products is subject to permanent quality checks.
The exact dosing of the individual ingredients has been carried out with Siwarex load cells from Siemens for more than ten years. A total of more than two dozen weighing stations, some of which are calibratable, are equipped with Siemens technology and integrated into the control system via Simatic I/O systems and controllers. “We have been very satisfied with the technology we have been using for years,” explains Markus Franzel, who is the responsible manager for EMSR (electrical, instrumentation and control) plant engineering at Tribotecc. “My team and I take care of the integration and modification of the Siemens weighing technology ourselves here in Arnoldstein.”
To this end, Franzel and colleagues visited Siemens’ Weighing Technology Center in Karlsruhe, Germany. Here, not only are Siwarex application possibilities shown in action, but customer-specific training courses are also held. “With the knowledge we gained, we were optimally equipped for the automation of our batching and weighing tasks,” Franzel recounts. “And if there are ever any unanswered questions,” he continues, “Siwarex Support is there to help us. Here, we always get competent answers at short notice from weighing specialists who know our application.”
New sieving technology
In the processing of a natural metal sulfide, an existing aggregate used to separate constituents was to be replaced by two sieving steps. “With this measure, we wanted to further improve product quality and operating principle of a bulk flowmeter: The impact force of the material deflects the baffle plate accordingly [Figure 1]. The processing electronics record the horizontal component of the reaction force and this signal is converted into a throughput quantity,” explains the manager for control technology and the modification. “However, the material feed is very tricky, because if it is overloaded, the sieve gets cracks and then the product quality is no longer guaranteed. In the worst case, the batch is lost.”
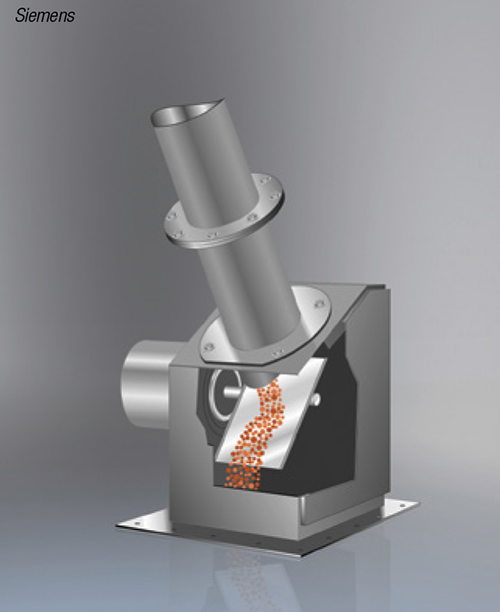
FIGURE 1. This diagram illustrates the operating principle of a bulk flowmeter. The impact force of the material deflects the baffle plate, and the processing electronics record the horizontal component of the reaction force. This signal is converted into a throughput quantity
The EMSR team solved this task with the help of three Sitrans WF300 series solids flowmeters from Siemens (Figure 2). For the flow measurement and the avoidance of sieve overloads, one solids flowmeter is responsible at Tribotecc. A second one is used for quality control. It is installed behind the sieve unit (Figure 3), so that a sieve rupture can be identified by detecting unexpected flowrates. “We have programmed the system in such a way that, in the event of a trend deviation, the dosing is automatically reduced in order to relieve the sieve or to be able to check it for mechanical damage,” explains Franzel, the principle.
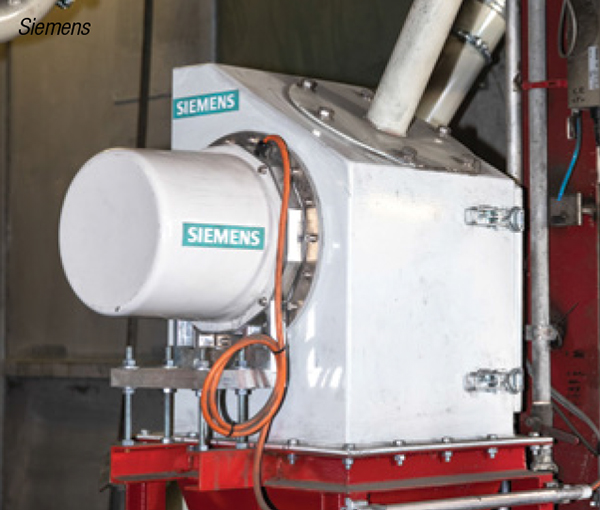
FIGURE 2. One of three bulk flowmeters of the Sitrans WF330 series is shown here. The weighing mechanism is externally mounted, which protects the flowmeters from dust, corrosion and wear
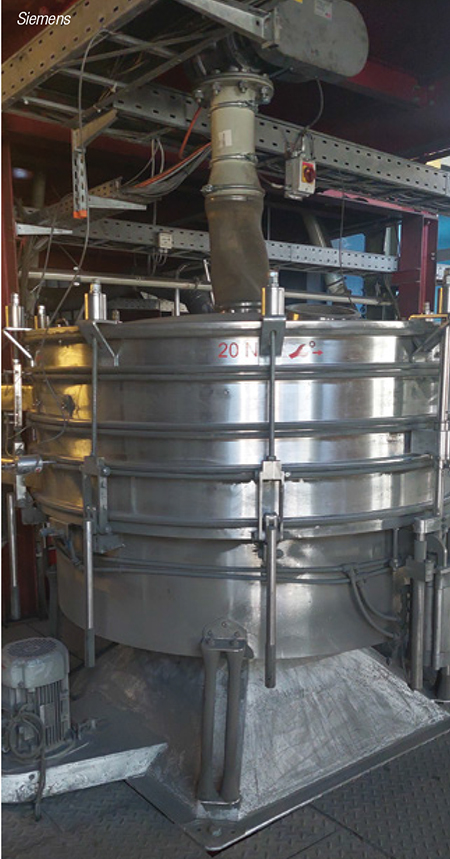
FIGURE 3. For continuous monitoring, one of the screens is supervised by WF330 bulk flowmeters for filling and filter rupture
Benefits
The solids flowmeters were to cover three application ranges: up to 2,600 kg/h, up to 1,200 kg/h and up to 450 kg/h. “The committed accuracy of±1% is crucial for our processes. The fact that we can now cover such a wide measuring range with the Siemens solids flowmeters and always precisely determine the throughput of the powder makes a significant contribution to maintaining our specified product quality,” says Franzel.
The load cells are connected via the Siwarex FTC (Flexible Technology for Continuous Weighing) function module. It can be clipped onto the backplane bus of Simatic ET 200 I/O systems with minimal cabling effort. The weighing module calculates and totals the flowrate and can be controlled via the existing Simatic S7-300 automation systems. “We did the integration via Siwatool,” reports the EMSR manager, adding with amusement, “It was smooth or — as we like to say at Tribotecc — absolutely frictionless.” The service software can be used to parameterize and adjust Siemens weighing systems, read out diagnostic messages and conveniently save or upload configuration files.
Tribotecc is very satisfied with the application of the three solids flowmeters, which now complement the extensive portfolio of Siemens weighing systems: “We achieve optimum throughputs in all application areas, our product quality benefits from precise weight measurement and we have monitoring of our sieves at the same time,” summarizes Franzel. ■
Edited by Gerald Ondrey
Author
Christoph Hillebrand is a product manager for Weighing Technology at Siemens AG (Munich, Germany; Phone: +49-800-22-55-336; Email: [email protected]; Website: www.siemens.com), and has worked at the Karlsruhe site for over 16 years. Prior to this, he also worked at Milltronics GmbH (now part of Siemens) and Rembe Safety + Control. Hillebrand has a Diplom-Ingenieur degree from the University of Paderborn.