With proper planning, spills can be managed properly and the risk of secondary events — which may be more dangerous and costly — can be reduced
Spills are probably one of the biggest problems any laboratory or pilot plant operation faces. While spills are often cited as a potential hazard, the actual mitigation steps are often very generic and ineffective, reflecting the often cursory nature of the hazard analysis and risk assessment in this area. After all, spills happen and just need to be cleaned up.
Spills — defined here as an uncontrolled release of liquids or solids into the operating space — are very common, due to accidents that happen during transportation, material transfer, maintenance, equipment failure and human error. Spills may involve hazardous or non-hazardous materials. Hazardous materials (those harmful to people or the environment due to their flammability, toxicity or corrosivity) are clearly the most dangerous. However, even spills of non-hazardous materials can create operating problems, damage equipment, and cost time and money to clean up.
Fortunately most spills in laboratories and pilot plants are minor — due to the relatively small volume of materials being handled — and just require some cleaning activities. However, some have resulted in fire and explosions, leading to both personnel injury and significant equipment and facilities damage. So more than cursory attention is warranted to minimize the risk of an unanticipated hazard (Figures 1 and 2).
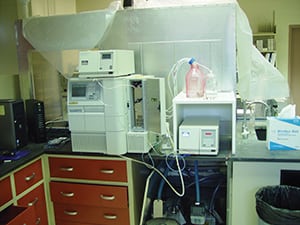
FIGURE 2. Without effective spill containment in place, any spills that might result from these vessels would likely fall to the floor and potentially find an ignition source in the vacuum pump and more fuel in the solvent container located nearby
Whenever possible, spill protection should be provided for all equipment and operations. This can range from permanent, expensive protection, such as dikes and berms for tanks, to simple pans, pails and trays for smaller equipment. The key requirement is the same in all cases — the spill protection must be large enough to contain the maximum probable spill.
For a batch system, this is generally straightforward. The volume of the largest single component (tank, reactor, sample cylinder, piping and so on) must be contained. However, splashing and fluid impulse (waves) that can occur when a liquid is released from its containment requires additional volume to be included in the spill-containment vessel, to prevent transient effects from overflowing the containment vessel. Typical industry guidelines suggest this volume must be increased by at least 10%. The higher the distance the spill may fall, the greater the velocity it will attain, and thus, the higher the containment volume necessary.
The closer the spill-containment vessel is to the source, the more momentum it will still have and again, the higher the containment.
Neither of these scenarios is subject to easy analysis, but the author’s experience with small systems suggests that sizing spill-containment vessels with excess capacity that is more on the order of 20–30% may be required for research-size laboratory and pilot systems. Paradoxically, smaller laboratory systems often require up to 50% extra volume.
Splashing from the added height is a definite issue and can result in significant amounts being cast outside the planned containment system. The amount of splashing or flowing over is important in determining safety. A few drops are unlikely to cause any issues. A few hundred cubic centimeters might be enough to find an ignition source or may pose a threat to personnel. A few liters is clearly an uncontained spill (Figure 3).
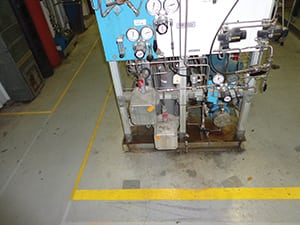
FIGURE 3. Shown here is an example of residual spill material remaining near a pilot plant pump. While trivial in itself, it does raise the potential for a fire to spread. One wonders if a simple drip pan could have eliminated the concern
For a continuous system, designing an appropriate spill-containment system becomes much more difficult. Either the spill containment must be sized for the total system’s volume — usually a physical or financial impossibility — or an appropriate alarm must be provided. Small laboratory systems may be able to capture the entire system’s contents, but even moderately sized pilot plants can begin to make this difficult or impossible. In these cases, the containment must be large enough to let the system or the operators respond effectively.
In the author’s experience, the time required for this response is often badly underestimated, particularly for manual responses. For this reason, automatic interlocks should be provided to rapidly shut down the source of the leak or spill, and any attendant dependent operations, immediately upon detection of a release. All too often, operators are temporarily absent or distracted, or fail to immediately recognize the problem and take effective action quickly enough, which leads to a larger spill. Systems that run unattended or off hours are particularly prone to major releases before the problem is discovered and corrected. Passing personnel and security guards can find it difficult to detect a spill until it has become so significant as to be blatantly obvious.
It is important to recognize that utility feed streams, often overlooked as non-hazardous, can also be the source of very expensive spills, as they effectively present a potentially unlimited supply in the event of a breach. For instance, water, chilled water, oil, steam and similar systems can produce large releases in the event of a leak or component failure.
Laboratory hoses that feed hood units, hoses and plastic piping that feed laboratory or pilot plant equipment, and booster pumps (or, more accurately, their seals) on similar pilot plant systems, are all potential sources of major spills (Figure 4).
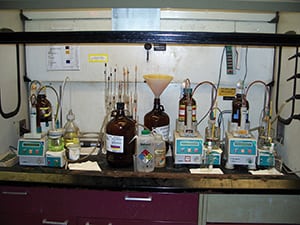
FIGURE 4. Shown here is an installation that relies on the laboratory hood for spill containment. The hazard analysis that had been carried out here was shortsighted, in that it only focused on the relatively low flowrates presented by the small volume of fluid, rather than on a potential incident that could result in an entire bottle breaking, releasing its contents
Similarly, laboratories on higher floors of a building are potentially at risk of causing major flood-related damage to equipment and facilities on lower floors. NFPA 45 Fire Protection for Laboratories Using Chemicals requires that all floor openings be sealed to prevent spills from spreading. Most building codes require similar measures but their focus tends to be on minimizing the spread of smoke or fire, not necessarily fluid spills.
NFPA 45 is careful to note that the spill protection must be compatible with the chemicals involved; if the containment system can be weakened or attacked after an exposure to the fluids in question, it must be repaired or replaced immediately. Sadly, most laboratories this author has seen over the past 40 years have had at least some areas that do not meet these criteria.
Unsealed or compromised penetrations between or behind laboratory benches go unnoticed. Modifications requiring floor or wall penetrations over time fail to be sealed or, at least, sealed effectively enough. Age and normal wear and tear result in compromised seals. In general, almost any large spill in a laboratory setting tends to find its way to lower floors and adjacent spaces unless the organization has an effective inspection and maintenance program in place — which is rare (Figures 5 and 6).
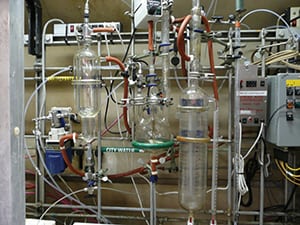
FIGURE 5. Laboratory settings typically have multiple sources of spills and nearby ignition sources, so relying on the hood alone for spill containment is usually not sufficient
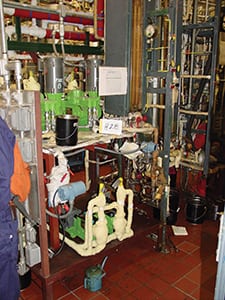
FIGURE 6. Even a well-designed pilot plant bay with floor drains will often have residual materials that could ignite near potential leaks and spill sources. If well maintained, as in this example, the residual risk should be minor
Many laboratories that handle only small amounts of hazardous materials fail to recognize that a break in a cooling hose to a glass heat exchanger in a laboratory hood could lead to several hundred gallons of water cascading down to lower floors overnight. The response time for guard tours off hours and even passing personnel during on hours is almost routinely grossly overestimated.
First the person must recognize the problem, then contact an individual capable of taking action or at least knowing what action to take. That individual must locate the source and determine how to safely shut it off. Rarely does this sequence take less than 15–30 minutes (often it takes longer). Aside from the obvious damage from the spilled liquid, there is also the potential for electrical shock if the liquid is conductive.
Retain the spill safely
The spill-containment device or system must be able to withstand the normal wear, tear and abuse of daily operations and still be viable when required. It is common to see lightweight pans and even permanent rails or sides in place, but badly damaged by routine traffic and noticeable bows, bends or crushed sections. Dikes and similar structures are often cracked. All may have unsealed penetrations, penetrations with compromised seals (for instance, seals that are cracked, oversized, crumbling and so on) that will compromise their effectiveness.
Portable spill protection (such as trays, pans, buckets and spill pallets) is subject to being bumped, moved or nudged out of its proper position due to routine operations and, more commonly, maintenance or modifications. Hence, the use of portable systems should require routine inspection and adjustment in their position if required. Sadly, it is often easy for a spill container to be slightly moved and not be noticeable although rendered significantly less effective. The best approach is to design a restraint or frame into which the container fits so that it cannot be moved out of place but can be lifted or slid out for emptying if necessary.
Permanent spill protection is prone to being rendered less effective by modifications that often move major sources within the frame without evaluating the effect on the existing spill containment. Problems can include the addition of other potential sources, which could require more containment. Examples include new equipment or sources of a potential release that are placed too close to the edge of the containment, leading to the potential for the momentum of the release carrying the spill over the containment, or new equipment or sources that are located higher off grade, creating more kinetic energy to allow a spill to flow up and over the containment.
In some cases, modifications may extend past the spill containment altogether. Hence, all such modifications should be reviewed for their effect on the spill containment and should be part of the organization’s management of change (MOC) process.
Maintenance often requires the removal of spill containment or at least parts of it. Yet, the potential for spills is often higher during maintenance-related activities. Hence the maintenance-activity plan should assess what temporary spill-protection measures are required.
The capacity and location of the spill-containment system also needs to evaluate the distance a leak or pressurized release could travel. Spill containment to capture a small slop stream running down the side of a drum or container usually does not need to be much bigger than the container. But spill containment for a small hole in a drum or a broken beaker can shoot out under head pressure and flow a much longer horizontal distance.
Plan for what happens next
For potentially flammable and combustible products, this requires that the spill containment be able to withstand a fire since this is always a possibility. Hence glass and plastic containers, soft-soldered trays, and similar low-melting temperature components are not suitable for laboratory operations. A contained fire is a hazard but an uncontained fire is always a major hazard.
Portable spill containment needs to be stable, so that when it is being filled or filling it cannot shift and result in liquid escaping. It must also be able to safely hold any debris that may be coincident with the spill, such as broken glassware or parts of a failed seal.
The work surfaces inside laboratory hoods are required to be fabricated so as to have some spill containment (for instance, in the form of a depression in the work surface, or by sealing around the edges to create a lip), in accordance with both industry standards and NFPA 45. However, many do not provide viable containment. Too often, the hoods were purchased without appropriate spill-containment capabilities, or were installed so that the containment is ineffective, or the existing containment has become compromised over time due to the loss of sealant, or scrapes, gouges or similar damage. Relying on a hood to contain a spill from equipment inside its interior, unless carefully tested in advance, is ill advised.
Absorbent pads, mats and temporary berms are valuable spill-containment tools. However, their capacity is limited so a careful assessment of their ultimate effectiveness for the duration of the spill is required. Too often, this author has seen almost total reliance on these inexpensive and easy measures which, upon analysis, can be shown to only provide limited mitigation, usually due to larger volumes of extended response periods. They are also often too easy to damage, leave gaps, or move and not be replaced during normal operations (Figure 7).
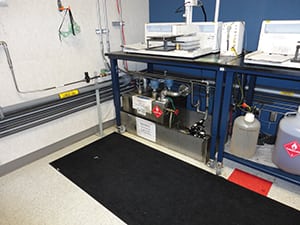
FIGURE 7. The spill containment on the left meets almost all the requirements for effectiveness, although it still requires manual clean up with a rag or absorbent pad. The area on the right, unfortunately lacks sufficient protection
Plan for safe final cleaning
Even simple laboratory pans and trays need to be selected and placed so that they can safely and easily be removed for emptying or arrangements can be made to allow cleaning in place. Larger trays and pans are often cumbersome, bulky and easily tipped when moving. The author has seen numerous trays, pans and containers that only transfer the spill from the source to an adjacent area due to difficulties in removal and handling.
As the spill containers get larger in size and volumes they become exponentially harder to handle or difficult to lift safely. Hence, prudent analysis may suggest that they need to be evaluated in terms of how they will ultimately be safely drained — even if this adds cost and complexity to the system design. In many cases, particularly on pilot plants or larger laboratory units, this may not prove feasible.
When this is the case, the hazard analysis and risk assessment should address any hazards of residual materials or difficulty in cleaning. At the very least, thought should be given to providing handles or similar means to allow personnel to lift and grasp the pan, tray or container safely. The potential weight it must carry should be evaluated and this often requires a stiffer or heaver pan to prevent it bowing or folding during movement when filled.
Trying to empty a pan or tray without a spout of similar directional pouring mechanism makes it more difficult and often results in secondary spills. Smaller trays can often use their square corners as these directional means to empty the collected liquids. However, larger trays and pans often require some thought and care in their selection or design to provide them. Otherwise pouring out the contents frequently becomes a spill-producing activity itself.
Permanent spill containment around pilot plants and support installations, such as tanks, requires a design that allows for easy cleaning. This usually means trying to design the containment with a slope to a low spot or sump that will allow collected fluids to be vacuumed or pumped out. Common assumptions that the operators can easily sweep the liquid to a collection point are almost always spurious and result in significant residual spillage remaining after cleaning. At best this is a housekeeping problem; at worst, it can create a standing unsafe condition. Many “portable” trays around pumps or small tanks fall into this category, because to actually remove them requires removing the equipment first, something rarely ever done in practice.
Many laboratory spill-containment installations fail badly on this point. For example, providing a larger pan to hold a hot plate or stirrer plus the contents of the container being heated or stirred is common and often the only practical approach. However, a large number of these installations will prove to be ineffective due to lack of proper analysis such as the following:
- Failure to account for the volume of the equipment, which leads to overflowing
- Failure to recognize that the spill, usually due to container failure (breakage) or upset (human error), will almost always result in the spill being splashed outside the container
- Failure to realize the container is too close to the sides of the containment (leading to the liquid momentum causing the spill to splash over) or too high above the spill containment (leading to the height giving the spill enough kinetic energy to splash out or flow over the containment sides)
- Failure to consider how the resultant spill, and debris can safely be separated and drained to a safe location
Review housekeeping efforts
Housekeeping procedures are an integral and critical part of proper spill containment. Any spill of flammable and combustible materials can lead to a fire. If the fire is contained, it can be extinguished more easily and with fewer consequences than if it is uncontained. In addition, a spill of a flammable or combustible liquid, if it reaches other combustible sources, can easily grow much larger. This means that a spill — or even a splashing — that ignites may be able to reach squeeze bottles of solvents, spare flammable or combustible chemicals, papers, lab notebooks, towels, or any of the other inevitable paraphernalia in a laboratory, causing the initial small fire to quickly grow into a large and dangerous conflagration. The author once saw a 500-ft 2 laboratory effectively burned out from a spill of only several hundred cubic centimeters of flammable liquids due to very poor housekeeping and a failure to recognize the numerous other “fuel” sources on nearby benches.
Poor housekeeping on a pilot plant (FIgure 8), particularly in terms of cleaning up all the residual materials from past spills, is critical in preventing a small flash-type fire that can easily damage other components and lead to a larger release (either spills or leakage). Similarly, keeping adjacent areas clear of other fuel sources, such as spare solvents, containers of feed or products, combustible materials and more, is also important in all cases, to make sure a fire stays localized and does not spread. The spill pan in a laboratory hood with the spare bottle of solvent right next to it rarely contains the secondary fire.
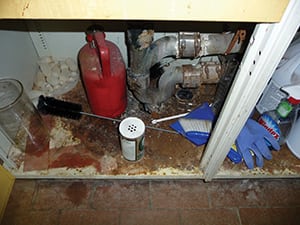
FIGURE 8. Shown here is an example of a spill that can easily leak through the unsealed hole around the drain beside it
Providing spill containment for an entire area, such as a laboratory or pilot plant bay, is a common technique. Although initially expensive to provide, it is often viewed as a low-maintenance, easy way to minimize the risk associated with potential spills. This is often not the case. To be safe and effective, a few key guidelines should be followed:
- The hazard analysis and risk assessment must evaluate the effects of any spill on all adjacent equipment and operations. At the least, it should evaluate the effect of a small fire spreading to numerous other fuel sources. This is more probable if the area does not have an electrical classification as Class I Division 1 or 2 or Zone 0, 1 or 2 (Figure 9)
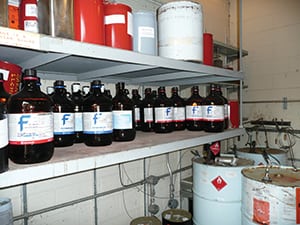
FIGURE 9. A risk assessment of this area would need to address the consequences of a smaller spill leading to a larger conflagration. While appropriately electrically classified to minimize the potential for ignition sources, the addition of a spill containment system on each shelf might significantly lower the consequences of any potential spill
- The construction of the area must address the need for sloping to the floor drains, if provided, or to a sump or similar low point for collection and ultimate removal of captured fluids. Often floor drains are poorly installed so that they either stand “proud” of the floor (that is, they stick up above the floor slightly), which makes drainage impossible. Or they are oplaced in small shallow depressions, which, in the event of a spill, would only provide drainage for a few inches beneath the drain. Many floor areas are essentially level or they slope slightly (and often imperceptibly to the eye) in several different directions, making it difficult to determine in advance where the spill will flow. If the area does not have floor drains, then consideration must be given to where the liquid will flow. If it flows under benches, hoods, and fixed equipment then cleaning will be difficult and probably poorly done leading to residual risk
- If floor drains are provided, they must drain to a safe location that can contain the spills and allow them to be transferred safely for proper disposal. Several common problems are often associated with these systems. For instance, a failure to provide adequate alarms allows them to overflow (usually due to an accumulation of numerous relatively trivial spills over time, or one larger spill that was bigger than originally envisioned). Similarly, placing a holding tank in a regular municipal sewer line and assuming that it can be isolated and taken off line before any contaminants escape is rarely a failsafe approach. The spill-reporting time may be longer than expected, the spill may go unreported, other non-hazardous drainage may sweep the tank constantly leading to contamination, or a similar issues may arise. Finally, providing a complex treatment or separation system that requires frequent maintenance and care can lead to frequent failure when it is forgotten or at least often neglected for a time.
Spills can also occur due to leakage from fittings, seals, gaskets and similar components. And they may arise due to normal operations that provide frequent repetitive opportunities for small, individually trivial spills to arise, as these can collectively accumulate over time to eventually reach critical levels. Situations in which this scenario can arise include: baths where containers or samples are frequently removed and often drip nearby; sampling where residual materials may continue to flow for a moment after completion; emptying containers into hazardous-waste cans for ultimate disposal with the attendant routine drips, splashes and trivial spills, emptying or filling smaller containers into or out of larger ones for ease of use or process needs with similar consequences; and other repetitive or routine operations.
Such occurrences can often make areas around these operations less safe, due to residual materials increasing the risk of a fire spreading, increasing the risk of personnel contact with toxic materials, or at least creating increased slipping and tripping hazards. In many cases, some local spill containment may be prudent to both restrict the area into which these minor spills could spread and make cleanup easier. This extra local containment is often much larger than the minor spills required to allow for a longer interval between cleaning or to address the potential for a larger-than-normal spill (Figure 10). Conversely, it may occasionally be much smaller than might be required in the event of a larger spill (such as a person dropping the container to be emptied). The potential for requiring a larger spill containment, to account for human error, should always be evaluated. For instance, the possibility of dropping a container that is being transferred from a bath to the bench next to it, overfilling a waste can or smaller container, dropping the larger container, and similar human errors should be assessed.
It is not always possible, nor is it always necessary, to provide spill containment around every potential source in a laboratory or on a pilot plant. However, the hazard analysis and risk assessment should make sure to look at the potential hazards from leaks and spills carefully — perhaps more carefully than it has been done historically — to make sure that they do not create unrecognized and unacceptable risks, or that providing spill protection of perhaps a different type might not help to further reduce an already low risk with minimal cost and operability impacts. The hazards we recognize and evaluate are the hazards we usually mitigate effectively; the hazards we overlook or consider trivial are usually the hazards that come back to create the accident.
Author
Richard P. Palluzi, P.E., CSP, of Richard P Palluzi LLC (72 Summit Dr., Basking Ridge, NJ 07920; Email: rpalluzi@verizon.net; Phone: 908-285-3782) is a consultant to the pilot plant and laboratory research community on safety, design and research project management. He retired as a Distinguished Engineering Associate after almost 40 years at ExxonMobil Research and Engineering, where he was involved in the design, construction, and support of pilot plants and laboratories for ExxonMobil’s research site in Clinton, N.J., as well as affiliates worldwide. Palluzi is the author of two books, and numerous articles and presentations. He is a past chair of the AIChE Pilot Plant Committee, ExxonMobil’s Pilot Plant and Laboratory Safety Standards Committee, and ExxonMobil’s Safe Operation Team for their Clinton Facility. He is on the National Fire Protection Association (NFPA) NFPA-45 Fire Protection for Laboratories Using Chemicals and NFPA-55 Industrial and Medical Gases committees. Palluzi also teaches several courses for the University of Wisconsin’s Dept. of Engineering Professional Development. He has B.E. and M.E. degrees in chemical engineering from Stevens Institute of Technology.