Ethylene is used almost exclusively as a building block — it is the largest-volume petrochemical produced worldwide (Figure 1). Production of ethylene grew rapidly in the middle of the 20th century, when oil and chemical companies began separating it from petroleum refinery waste gas and producing it from natural gas and ethane (obtained from byproduct refinery streams).
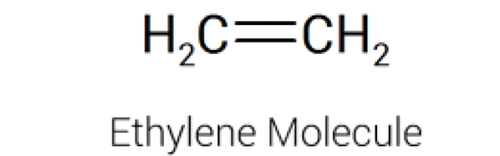
FIGURE 1. Ethylene is the most produced petrochemical worldwide, by volume
Ethylene is mostly used as a raw material for the production of polymers and other organic chemicals in consumable end uses, especially packaging. Polyethylene (PE) is responsible for about 60% of global ethylene demand. The main class of PE produced in the world is high-density polyethylene (HDPE), which is responsible for the consumption of one-third of the available ethylene. This is followed by low-density polyethylene (LDPE) and linear low-density (LLDPE) varieties.
Ethylene is stored as a liquid under high pressure or at low temperatures. However, most of the time, ethylene is directly supplied to consumers, via pipeline grids.
Steam cracking
Steam cracking — high temperature pyrolysis in the presence of steam — is the main technology used to make ethylene. The petroleum-based feedstocks used in steam cracking are grouped as gaseous (ethane, propane, n-butane, natural gas liquids and any mixture of them) and liquid (field condensates, natural gasoline, benzene, toluene, xylenes, raffinate, naphtha). Different feedstocks and cracking conditions generate different product slates. In general, high yields of ethylene with small amounts of byproducts are obtained from gaseous feedstocks, while lower ethylene yields with larger amounts of byproducts are obtained from cracking liquid feedstocks.
Process
Production of polymer-grade (PG) ethylene from ethane feedstock can be divided in three main parts: cracking and quenching; compression and drying; and separation (Figure 2).
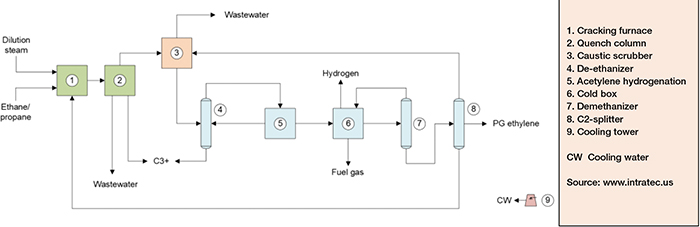
FIGURE 2. The diagram shows the process for producing ethylene by cracking ethane
Cracking and quenching. Ethane and dilute steam are fed to furnaces in which, under high-severity conditions, ethane is cracked, forming ethylene and some byproducts. The furnace outlet stream is subsequently fed to a water-based quench, to prevent further reactions and formation of undesirable byproducts. From the quench tower, the cracked gas is directed to compression and drying.
Compression and drying. The compression of the cracked gas is performed across five stages. After the third stage of compression, carbon dioxide and sulfur are removed from cracked gas by caustic soda and water washes in a caustic scrubber.
Separation. After caustic wash, the cracked gas is sent to a fourth compression stage and then fed into a column for removing C3+ hydrocarbons. The overheads product from this column, composed primarily of ethylene and ethane, is fed to the last compression stage. The compressed gas is fed to an acetylene converter and then to a cold box for hydrogen and light hydrocarbons removal, ensuring that ethylene losses are minimal. At this point, the product from the chilling train is fed to two further separation columns. In the first column, methane is obtained from the top and further used in the cold box, while the bottom stream is fractionated in the C2-splitter. In this column, high-purity ethylene is drawn from the column as a side stream. Ethane, from the C2-splitter bottom, is recycled to the cracking furnaces.
Economics
Most recently, growing environmental concerns have increased interest in alternative routes to conventional petroleum-based ethylene production, especially the dehydration of bio-derived ethanol. With such a diverse range of derivative products, ethylene demand is highly sensitive to economic cycles. In fact, it is often used as a reference in the performance evaluation of the petrochemical industry. The economics of ethylene production is largely dependent on the prices for feedstocks and co-products (mainly propylene). In general, heavier feeds lead to higher production costs and capital investment required.
Editor’s note: The content for this column is developed by Intratec Solutions LLC (Houston; www.intratec.us) and edited by Chemical Engineering. The analyses and models presented are based on publicly available and non-confidential information. The content represents the opinions of Intratec only.