These key elements of internal boiler feedwater (BFW) treatment will help avoid boiler tube failures due to scale and pitting
For many chemical processes, an industrial packaged-type boiler is a critical component for either power generation or for producing steam. In the event that boilers are taken offline due to a failure, the facility may experience a loss of power or production downtime, each carrying significant economic consequences. Improper treatment of boiler feedwater can result in boiler tube failures due to oxygen pitting and scale buildup on internal heating surfaces. This article provides an overview of proper boiler feedwater treatment to help plants avoid failures.
Boiler feedwater treatment typically comprises a combination of several different processes, each designed to remove certain contaminants from raw make-up water or condensate return water. These processes can be divided into two parts: an upstream water-treatment system and a chemical treatment program. The upstream processes can include a combination of filtration, water softening, demineralization, reverse osmosis and de-aeration, depending on the quality of the raw water used. The chemical treatment program would include the introduction of chemicals to the boiler water to remove any remaining unwanted contaminants from the pressure vessel itself.
In this article, the primary focus is on the de-aeration process and the chemical treatment program.
Boiler feedwater options
For any commercial or industrial boiler-type application, the boiler feedwater can include raw make-up water, condensate return, or any combination of the two. Raw make-up water is defined as freshwater introduced into the system to account for losses in water or steam due to consumption by the process or from wastewater that is removed from the system. Condensate return water refers to water that has been condensed from the boiler steam after it has delivered heat to the process, and is then recycled back to the feedwater system.
For any application, the conservation of condensate return is ideal. Even though the condensate has lost some energy through the process, it is typically at a higher temperature (greater than 120°F, for example), and contains more energy than the raw make-up water (typically around 40–50°F). Note that regardless of how much condensate can be recovered, every application is going to require some make-up water due to losses throughout the system.
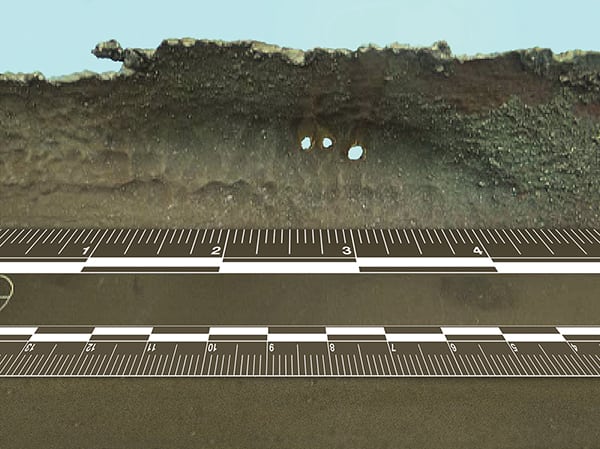
Figure 1. Pitting on the internal surface of a tube can result from the presence of oxygen in the boiler feedwater
De-aeration
De-aeration is a critical feedwater treatment component for every boiler application. The raw make-up water fed from the upstream water-treatment system is saturated with oxygen. Because the industry standard for boiler components and piping is to use carbon-steel materials, oxygen in the water will cause extensive corrosion to the components if it is not removed. Typical damage to any carbon-steel materials, including piping, boiler tubes and drums, will include pitting and thinning of the components due to the oxygen attacking the iron in the carbon steel (Figure 1). This pitting is a result of the basic reaction for the formation of rust (Equations (1) and (2)).
4Fe + 6H2O + 3O2 → 4Fe(OH)3 (1)
2Fe(OH)3 → Fe2O3 + 3H2O (2)
These reactions remove material from the carbon-steel heating surface and can create deposits that can collect on the internal surfaces. These deposits reduce heat-transfer efficiency and can also plug the tubes, which creates potential hot spots that can lead to tube failures.
It may not seem that these reactions could pose such a threat to the boiler equipment. However, given that typical industrial packaged-type boilers can generate from 10,000 lb/h to more than 250,000 lb/h of steam, this type of flow would expose the boiler to a great deal of oxygenated water, and could result in corrosion and potential tube failures in a fairly short period of time.
In order to remove oxygen from the water and mitigate the risk of corrosion, there are two methods of de-aeration that can be used in combination with each other. The first is to use a piece of equipment that is referred to as a de-aerator, and the second is to use an oxygen scavenging chemical to remove any remaining oxygen from the system.
A de-aerator is used for virtually every boiler application at some stage during the feedwater treatment process. There are two designs that typically are used, a spray type and a tray type de-aerator (Figure 2), which, for the purposes of this discussion, provide essentially the same end result.
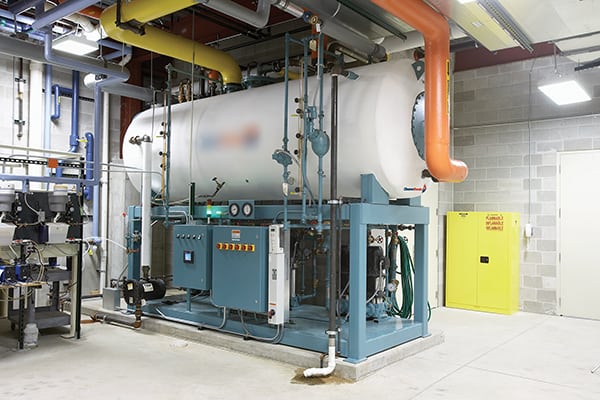
Figure 2. Tray-type de-aerators are designed to remove oxygen from boiler feedwater to avoid corrosion issues
A de-aerator uses a combination of steam heating and turbulent mixing to remove the oxygen from the water to a level of 0.007 parts per million (ppm), as recommended by the American Society of Mechical Engineers (ASME) Water Quality Guidelines (Table 1). Note that the table shown here is abbreviated, and that the complete table includes recommended values all the way up to 2,000 psig.
In a tray-type de-aerator, the raw make-up water is sprayed into the top of the de-aerator column by means of a spring-operated sprayer or by spray nozzles. The spraying action generates small water droplets or a film, which flow downward between trays or deflection baffles. To avoid corrosion, the interior of the de-aerator includes stainless-steel materials for any wetted parts that come into contact with the oxygen-rich make-up water. The steam used to heat the water enters the de-aerator in the lower part of the tray section and rises through the sprayed water in a countercurrent-flow manner. As the steam and water mix, the incoming make-up water is heated from the typical inlet temperature of 40–50°F to the saturation temperature in the de-aerator, and the oxygen is driven out of the water as a result of the heating and mixing. The oxygen is allowed to vent to atmosphere from the top of the de-aerator. The steam is condensed into the make-up water as it transfers heat, and the mixture then flows downward into a feedwater storage tank. Note that the saturation temperature of the tank may vary depending on the specific operating pressure of the de-aerator. Typically, these are operated at pressures of 5–15 psig and temperatures of 228–250°F. The relationship between the oxygen saturation content in the water and the water temperature is demonstrated in Figure 3.
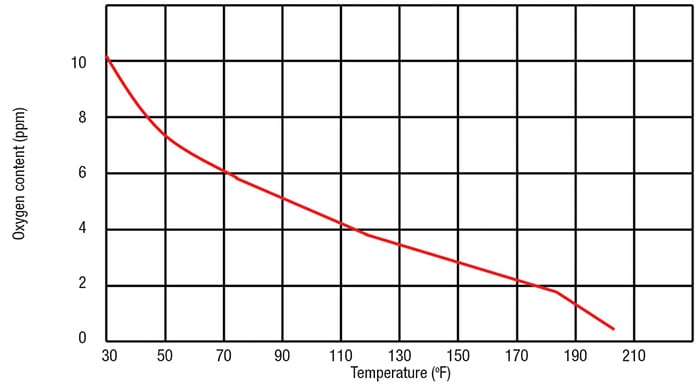
Figure 3. The relationship between oxygen content in the feedwater and temperature is shown here
Oxygen scavenging
Even after the reduction in oxygen from the de-aerator, there is still a small amount of oxygen remaining in the feedwater, and this is enough to cause corrosion. In order to remove this residual oxygen, the de-aerator can be supplemented with an oxygen-scavenging chemical. The typical system includes carbon-steel materials for the feedwater storage tank, feedwater pumps, piping between the de-aerator and the boiler, and boiler pressure parts. All of these materials would be subject to corrosion if the remaining oxygen is not removed. Because all equipment downstream of the de-aerator is made from carbon steel, the oxygen scavenger should be introduced as far upstream as possible, in the feedwater storage tank that is directly connected to the de-aerator itself.
Three of the most common types of chemical treatment used for oxygen scavenging are sodium sulfite, hydrazine and carbohydrazide. Each of these chemicals provides different benefits that should be considered before selecting which oxygen scavenger should be used for a particular application.
Sodium sulfite. Sodium sulfite typically comes as a powder or in an aqueous solution, and is generally the most economical chemical used for oxygen scavenging. The sulfite is very effective and reacts with the dissolved oxygen in the water according to the reaction shown in Equation (3), removing the oxygen from the system. With this chemical reaction, the sulfite attacks the oxygen at a ratio (dosage) of approximately 7.5 parts sulfite to 1 part oxygen.
2Na2SO3 + O2 → 2Na2SO4 (3)
In this reaction, the sulfite and oxygen form a solid sodium sulfate product, which is carried through in the feedwater. The solid must be removed from the boiler water via the blowdown that is discharged from the boiler system as wastewater (Figure 4). Depending on the specific requirements of an application, this can be one of the drawbacks to using sodium sulfite — this end product adds to the overall solids concentration in the boiler water. With higher-pressure boilers, or boilers that are generating steam to drive turbines, maintaining a low solids content in the steam is more critical, and the use of a sulfite scavenger would not be recommended in those cases.
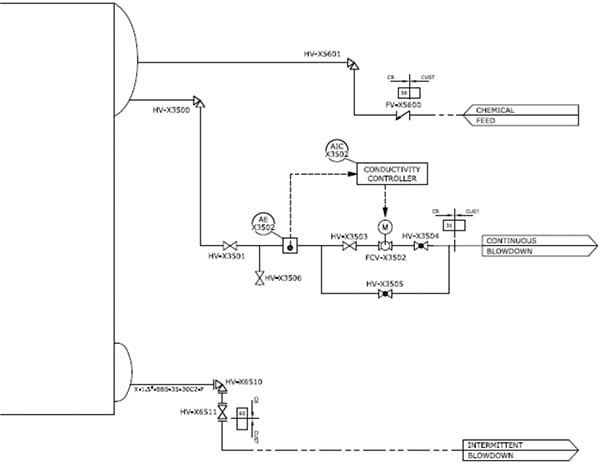
Figure 4. The diagram shows a typical boiler blowdown configuration
Another factor to note is that the sulfite can break down and react with the water at lower pressures (less than or equal to 600 psig), forming sulfur dioxide and/or hydrogen sulfide. These two gases are carried through the system in the outlet steam, reducing the alkalinity of the steam and any condensate return. This low alkalinity causes acidic conditions downstream of the boiler, and can result in corrosion to the system.
One last item that should be considered regarding protection of the materials downstream of the boiler is that the sodium sulfite is nonvolatile, and would not be carried in the boiler steam throughout the system like the sulfur-containing gases would. Therefore, using sodium sulfite as an oxygen scavenger would not provide the benefit of protecting the materials downstream of the boiler, including any condensate that may be part of the boiler feed system.
Hydrazine. Hydrazine is the second option that may be used for oxygen scavenging. This chemical comes as a colorless liquid and also can be added directly to the feedwater storage tank upstream of the boiler. The hydrazine reacts with the remaining oxygen in the feedwater according to the reaction shown in Equation (4). The hydrazine attacks dissolved oxygen at a ratio of 1 part hydrazine to 1 part oxygen.
N2H4 + O2 → N2 + 2H2O (4)
The products of the reaction are simply nitrogen and water, so this scavenger does not add any solids content to the boiler system and does not impact the boiler blowdown rate. This makes hydrazine a better choice for any applications where lower solids content in the steam must be maintained. Also, because the hydrazine does not create any corrosive gases that can be carried through, the alkalinity of the boiler system is not affected by the use of this chemical.
Something that must be considered when using hydrazine is that if the given application calls for steam that is greater than 750°F, the hydrazine will start to break down and form ammonia. Depending on the trim and valve selections for the boiler and low-pressure feedwater system, the presence of ammonia can cause potential issues. Ammonia will attack any “yellow metals,” or metals containing copper. This possibility must be considered in the design of any new systems, as well as existing systems that may use these types of materials.
Carbohydrazide. The third oxygen-scavenging chemical to discuss here is carbohydrazide. The reaction between carbohydrazide and oxygen is shown in Equation (5). The reaction is ideal, as it can be achieved at fairly low pressures and temperatures as seen in a typical deaerator. Similar to hydrazine, the lower molecular weight of carbohydrazide makes it able to react at a ratio of 1.4 parts carbohydrazide to 1 part oxygen.
H6N4CO + 2O2 → CO2 + 2N2 + 3H2O (5)
This reaction also does not generate solids, so the boiler blowdown rate is not affected by this scavenger. One benefit that carbohydrazide offers, but hydrazine does not, is that it is volatile. Any carbohydrazide that is remaining in the water can be carried by the steam out of the boiler, which helps to protect any carbon-steel materials in the downstream system. It is important to be aware that this carbohydrazide can break down to hydrazine at higher temperatures (higher than 350°F). However, given the typical operating conditions of a de-aerator (228–250°F), this should not be an issue if injected directly into the feedwater storage tank, where it can react prior to being heated to above this 350ºF threshold in the boiler.
The three chemicals discussed here are considered to be among the most commonly used oxygen scavengers for industrial boiler systems. Each of the chemicals is capable of removing residual oxygen from the boiler feedwater, but should be evaluated based on its individual benefits. Beyond these three, there are also several other oxygen-scavenging chemicals used. It is recommended to coordinate the use of these chemicals with a local water-treatment or chemical provider based on the specific water quality in a given plant.
Treatment for scale and solids
In addition to de-aeration and oxygen scavenging, boiler feedwater typically requires additional chemical treatment for the removal of solids that are left in the water after going through the upstream treatment system. These solids can include silica, calcium and magnesium compounds, and various others that contribute to the hardness of the water. Removing these solids helps to mitigate the risk of scaling and deposits collecting on the heat-transfer surfaces. Scale is formed when the water boils off of the heat-transfer surface and solids are left to precipitate out, sticking to the surface. In an industrial boiler, this scale would occur on the internal surfaces of the boiler tubes and drums. As the scale builds over time, deposits collect on the surfaces, causing fouling, which at a minimum, reduces heat-transfer efficiency. In extreme cases, the deposits can actually clog or plug the boiler tubes. This creates hot spots in the tubes due to a lack of circulation (water cooling), and may cause them to rupture. If a tube failure occurs, this is likely to require significant downtime and potentially costly tube-replacement work.
There are three primary chemicals that are used to treat water hardness. These typically include the use of a phosphate or a chelant in combination with a polymer. The appropriate combination of these would be project-specific, depending on specific water quality and the water-treatment philosophy and standards of the facility. The phosphate treatment reacts with the scale-causing minerals, such as calcium and magnesium salts, and precipitates the hardness out of the water, since the products are insoluble. Chelant treatment is slightly different — the products of the reactions form soluble structures that remain in the water and do not collect on the heat-transfer surfaces.
Both the phosphate and chelant treatments usually are supplemented with a polymer, which acts as a dispersant. The polymer prevents either the precipitated or soluble materials from collecting on surfaces and forming scale or buildup of deposits. The products of either of these treatments form a sludge that typically settles into the upper and lower drums of the boiler. Because the sludge has been conditioned by the addition of the polymer, it does not adhere to the surfaces and is removed via continuous or intermittent blowdown. The rate of blowdown required for removing this sludge can be set using manual valves, or can be monitored and modulated with the use of a conductivity controller.
Phosphate treatment
When using phosphates for water treatment, the precipitation of calcium and magnesium compounds are achieved through a number of reactions that can occur in combination with each other. These reactions are possible with the heating of the boiler water and the presence of calcium, sodium and magnesium. Several intermediate hydroxide and carbonate products can be formed due to the heating of the boiler water and the potential for carbon dioxide to be present. The reaction with the phosphate occurs when both calcium and magnesium are present as bicarbonates [Equations (6) and (7)].
3Ca(HCO3)2 + 2H3PO4 → Ca3(PO4)2 + 6H2O + 6CO2 (6)
Mg(HCO3)2 + 2Ca(OH)2 → Mg(OH)2– + 2CaCO3– + 2H2O (7)
For the calcium reaction, the desired end product is calcium phosphate, where the initial magnesium reaction forms a magnesium hydroxide. Both of these products will precipitate out of the boiler water and can be removed from the boiler with the blowdown. If silica is present, it is preferred that the magnesium hydroxide undergo a second reaction to form magnesium silicate. With this, both the magnesium and silica would be able to precipitate out of the boiler feedwater. One of the benefits of phosphate treatment is that it helps to maintain sufficient alkalinity for this reaction to take place. The phosphate treatment would be supplemented with a polymer to condition the solids to remain dispersed in the water until they settle to the bottom of the drum for removal with the blowdown.
Chelant treatment
A chelant is a molecule that is able to bind to a positively charged metal ion (cation). This type of chemical treatment involves the introduction of a fairly weak organic acid that is able to react with the calcium, magnesium and other metals in the water. Once this reaction has occurred, the resulting product is unable to deposit itself on the boiler heating surfaces because it is soluble in the water. Similar to the phosphate treatment, a supplemental polymer also would be added to act as a dispersant to allow the deposits to settle in the drum(s) for removal with the blowdown.
Two common chelants that are used for boiler feedwater treatment are nitrilotriacetic acid (NTA) and ethylenediaminetetraacetic acid (EDTA), shown in Figure 5.
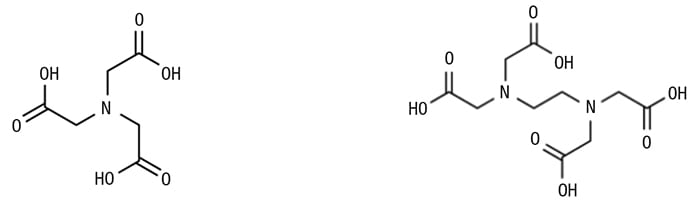
Figure 5. Molecules such as nitriloacetic acid (NTA; left) and ethylenediaminetetraacetic acid (EDTA; right) can chelate scale-causing minerals to prevent them from precipitating on heat-transfer surfaces
Both of these are very effective at binding with the metals in the water, as they each contain multiple reaction sites. NTA contains four sites (1 N + 3 OH), and EDTA contains six sites (2 N + 4 OH). Both chemicals form a ring-like structure when they react with the metals, and react on a mole-to-mole basis [Equations (8) to (13)].
Ca+2 + NTA–3 → CaNTA– (8)
Mg+2 + NTA–3 → MgNTA– (9)
Fe+3 + NTA–3 → FeNTA (10)
Ca+2 + EDTA–4 → CaEDTA–2 (11)
Mg+2 + EDTA–4 → MgEDTA–2 (12)
Fe+3 + EDTA–4 → FeEDTA– (13)
Note that with these two chemicals, the EDTA will form a more stable ring structure around the metal atoms, because it has the two additional reaction sites. The NTA only is able to react at four sites, which makes the product more vulnerable to additional reactions with other negatively charged ions.
Similar to the oxygen scavenging chemical treatments discussed, the combinations of phosphate-polymer and chelant-polymer chemicals discussed here are considered to be among the most commonly used. Again, it would be recommended to coordinate the use of any chemicals with a local water-treatment or chemical provider based on your plant’s specific water quality.
Concluding remarks
The chemical treatment required for boiler feedwater in any facility is dependent on the specific water quality at the given site and may require additional treatment outside of what was identified here. Boiler feedwater at any facility should be analyzed chemically and compared to the ASME Water Quality Guidelines to determine which chemical treatment options may be necessary, and which would best comply with the facility’s water treatment program and philosophy.
Edited by Scott Jenkins
Author
Dan Skiles is an application sales engineer at Cleaver-Brooks – Engineered Boiler Systems Group (6940 Cornhusker Highway, Lincoln, NE 68507; Email: [email protected]). Skiles currently works in the sales department, where new project requests for quotations are reviewed, and the boiler systems are initially designed. He received a B.S. in chemical engineering from the University of Nebraska in 2007 and has worked with Cleaver-Brooks since that time.