Although waste is unavoidable in industrial processes, many companies are turning toward business strategies that seek to treat waste with minimal environmental impact — or even better, prevent waste altogether
In the past, waste was simply discharged without any treatment. This occurred until authorities began enforcing regulations. Early regulations proved to be successful in reducing waste streams. However, current challenges related to declining resources and increasing energy costs require a different and more proactive approach to waste. In some cases, waste streams might prove to be a valuable product, and waste minimization, as well as energy efficiency, may be game-changing advantages for an organization. Waste minimization can be part of project execution for new-build installations, as well as revamps of existing facilities. Multidisciplinary teams can select activities to minimize waste and enhance cost efficiency. Overall, companies that invest in waste minimization as part of a sustainability strategy can financially outperform competitors who follow a less sustainable agenda.
Past practices
The industry’s emphasis on waste treatment is relatively new, but industrial waste itself has a long, messy history. At the beginning of the previous century, the policy adopted by the chemicals industry for waste handling was to either dilute or isolate the waste stream [ 1]. The common practice was to discharge liquid waste into rivers or other water bodies for dilution and then let nature do its work. The common belief in industry was that “natural purification” would solve the problem of toxic substances in waste streams. Isolation as a policy involved selecting a remote location far away from the public to avoid nuisance and discharge the untreated waste into rivers or to the atmosphere. These policies increasingly caused problems, as the pollution of water bodies affected the public water supply, and also as urbanization expanded near production sites.
Protection of the environment was of less importance in the past. However, under pressure from public and environmental institutions, things changed. U.S. Congress prohibited dumping oil waste into marine environments in 1924. Supervisory water boards started questioning the practice of discharging liquid waste into rivers and water bodies. Some companies were reluctant to incorporate waste treatment in those days, claiming that the costs were too high or that appropriate technology was not available. However, in the 1930s, many waste-treatment capabilities were indeed readily available. Representatives of waste-treatment providers claimed: “There is no waste discharged for which there is not a treatment,” and added “what may at first seem to be an exorbitant expense in order to stop polluting, a stream may prove to be a boon to a plant by the proof to the owner that he is throwing away a product that may be of value” [ 1].
Nonetheless, dumping hazardous waste in pits and lagoons remained the most common practice until the 1970s. Companies would do this partially on their own property, if there was enough space, and partially on the property of others, transferring liability to other parties, as in the case of Love Canal, N.Y. [ 2].
Progress is made
These practices were not sustainable, and under the pressure of public opinion and regulatory bodies, legislation was introduced to prevent pollution of soil, water and air. This occurred in all industrialized countries comprising the Organization for Economic Co-operation and Development (OECD; Paris, France; www.oecd.org). Waste philosophy changed, and the waste hierarchy was introduced. The waste hierarchy in the U.S. is provided by the Environmental Protection Agency’s (EPA; Washington, D.C.; www.epa.gov) Sustainable Materials Management: Non-Hazardous Materials and Waste Management Hierarchy. In Europe, the European Union (E.U.) Waste Hierarchy approach was adopted in the Waste Framework Directive (2008/98/EC), which, by itself, dates back to 1975. The approach is illustrated in Figure 1.
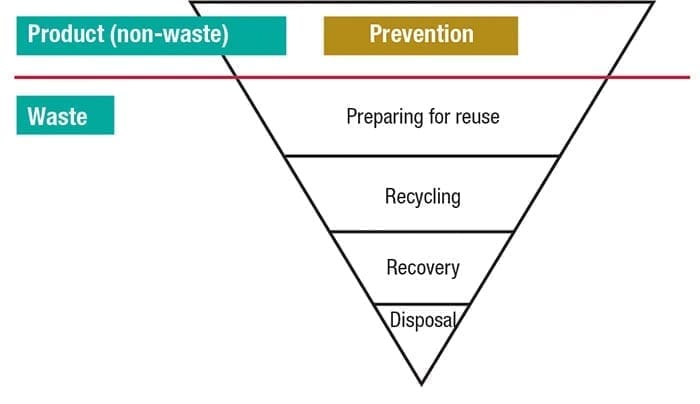
FIGURE 1. The E.U. Waste Hierarchy provides guidance on best practices for handling industrial waste
The philosophy worked. As evidence of this, the total petroleum hydrocarbons (TPH) discharged from European refineries has declined significantly since the 1970s, as reported by Concawe [ 3] and depicted in Figure 2.
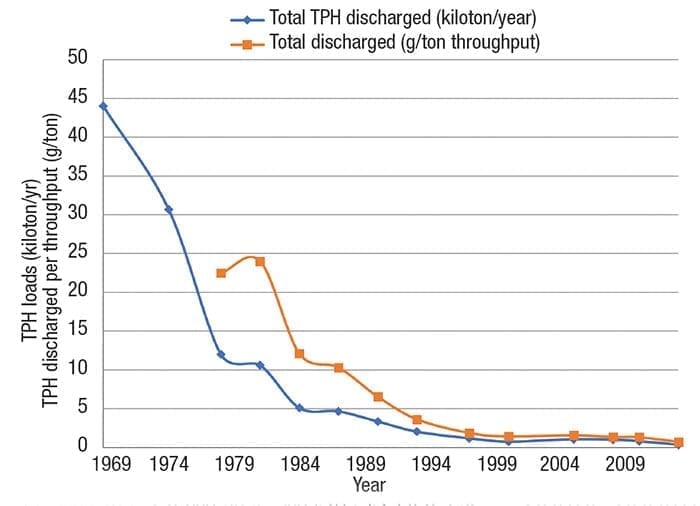
FIGURE 2. Coinciding with the introduction of waste hierarchy principles, total petroleum hydrocarbons (TPH) loadings and effluent rates have trended downwards significantly since the 1970s [3]
Over the same period, the total quantity of wastewater discharged from E.U. refineries declined from 3.12 billion to 0.24 billion m³/yr in 2013 [ 4]. However, the relative, as well as absolute, quantity of hazardous waste over the same period increased to 1.07 ton/kiloton of waste versus throughput in 2013. For non-hazardous waste, the average quantity in the same year is 1.45 ton/kiloton throughput. The rise in production of hazardous waste can be explained by the proliferation of waste-emission-control facilities, such as three-stage wastewater treatment and the consequent rise in biological sludge production; or the increased use of electrostatic precipitators (ESP) to remove dust from fluegases; or an expansion in the tonnage of material removed during remediation activities [ 4]. Sludge and spent chemicals, including acids and bases, are the main volume of the produced waste in petroleum refineries (typically around 45% and 14%, respectively). Over the reported period between 1993 and 2013, the percentage of total disposed waste to landfill reduced from 40 to 20%. In parallel, the recycled waste increased from 18 to 34% [ 4]. Meanwhile, the total costs for waste disposal at E.U. refineries increased from $80 million to $137.2 million per year. These are simply the costs for disposal of the waste. The true cost of waste is much higher, and includes not only disposal costs, but also purchase cost of materials, handling and processing costs, management time, monitoring costs, lost revenue, any potential liabilities and post-disposal segregation activities [ 5].
Finding value in waste
Since the 1970s, much progress has been made in waste treatment. Technology has matured and proven to be successful in reducing pollution. Waste typically has a negative connotation — nonetheless, waste can also have added value if used as a feedstock for other industrial processes. What was considered a waste stream in the past can actually be useful for certain purposes. Most refineries have included process units to treat the bottom of the barrel contents, which were previously seen as waste, producing more clean fuels and valuable products. In another example, desulfurization of natural gas and fuels generates cash flow, and has even supplanted more traditional sulfur sources, such as the Frasch process from mining operations, as the main source of raw materials in the sulfur market (Figure 3).
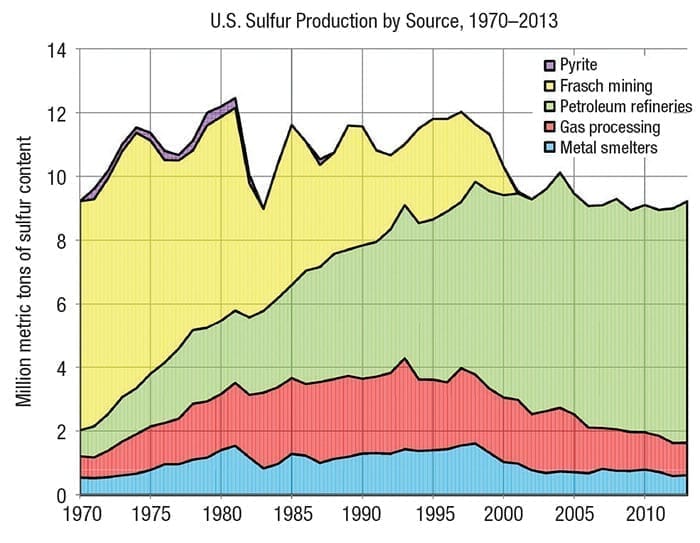
FIGURE 3. Sulfur is one example of a market where what was previously considered to be a waste-treatment operation (desulfurization units in natural gas processing) actually produces a useful raw material [6]
Another example of waste re-purposing is petroleum coke (petcoke), which is a byproduct of extracting and processing certain types of crude petroleum. Previously seen as a waste stream that must be sent for disposal, the market for petcoke is now expected to surpass $25 billion by 2024 as co-incineration feed in coal-fired power plants [ 7]. All of these efforts were enforced by regulations, but clearly show that there are benefits to be earned in being more mindful about waste streams. As the supply of resources becomes more uncertain, minimizing waste and making more efficient use of resources as part of an overall sustainability strategy will benefit every company.
Prevention and minimization
On top of the waste hierarchy pyramid are prevention and minimization. The best waste-treatment strategy is to not produce any waste. To enable waste minimization, there should be a shift from end-of-pipe treatment activities to adopting inherently sustainable processes throughout a facility (Figure 4). However, these efforts require careful planning and engineering. During the early phases of a project, decisions are made that affect the quantity and composition of waste. However, waste is not exclusively produced during the operational phase of the facility. Each phase of the project, such as construction, commissioning and startup, can be included in waste-management planning. A waste minimization strategy is not difficult to execute — it simply needs appropriate attention and leadership.
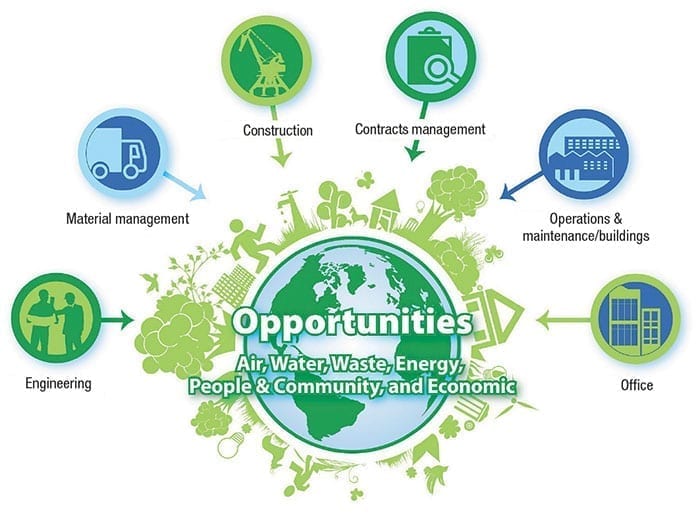
FIGURE 4. There are opportunities to enact more sustainable operations at every level of an organization and throughout the entire lifecycle of a project [8]
There are many ways to incorporate waste minimization into a project. To succeed, sustainability efforts need to be a management priority, with clear support from a company’s leadership [ 9]. Sustainability efforts can be implemented in both new-build and in revamp projects. Activities regarding sustainability should be assigned to a sustainability coordinator. For each project phase, a multidisciplinary team can select the most appropriate activities to devise fit-for-project solutions that serve the environment while maintaining the project’s budget and operational efficiency. The engineering, procurement and construction (EPC) contractor can help support this effort by providing their expertise and knowledge of project execution. A sample of these activities are summarized in the following sections.
Engineering.Selection of licenses is part of the process to minimize waste. During this process, not only capital expenditure (CAPEX) considerations should prevail, but also operating expenditure (OPEX) and costs of waste disposal and energy usage. Assuming the installation will be in operation for at least 20 years, the costs for resources, disposal of waste and energy consumption can have a significant impact on operational costs.
Material management.Receiving materials and equipment in the warehouses and laydown areas during the construction phase of the project produces large quantities of shipping packaging. Specifying packaging materials during the procurement of the materials and equipment can avoid significant efforts related to sorting packaging waste onsite and ensures the best possible disposal route — preferably for reuse or energy recovery.
Construction.Select modularization techniques to build a large portion of the project offsite in dedicated workshops — where waste can be better controlled, recycled and reused. Modularization can reduce the activities onsite and require less shipping-related packaging in comparison to having materials delivered separately for stick-built installations.
Contracts. Companies should require contractors to have a sustainability plan submitted as part of their technical proposal that is evaluated as part of an award recommendation. This plan would include items such as the following:
- Water usage and recovery plan
- Energy and power usage plan
- Recycle or reuse plan for permanent and temporary construction materials
- Dust control plan
- Hazardous and toxic waste disposal plan
- Transportation plan
You may wonder: Why should I do this? The answer to this question is very simple — it’s good for business. Considering waste minimization as part of a sustainability strategy provides a competitive advantage for the company [ 9]. A comparison made between companies operating in similar sectors (including chemicals manufacturing) with and without a strong sustainability agenda showed a considerable difference in financial performance. Companies that are more advanced in sustainability matters also have a higher return on assets (34%) and return on equity (16%) [ 10]. This improved performance can be attributed greatly to waste minimization and more efficient use of resources. Financial incentives are not the only benefits that come with a comprehensive sustainability strategy. Corporate image can be strengthened, as well, by showing the company’s commitment to improve its sustainability. ■
Edited by Mary Page Bailey
References
1. Colten, C.E., Creating a Toxic Landscape: Chemical Waste Disposal Policy and Practice, 1900–1960. Environmental History Review, vol. 18, no. 1, 1994, pp. 85–116. JSTOR, www.jstor.org/stable/3984746.
2. Beck, E.C., The Love Canal Tragedy, EPA Journal, January 1979.
3. Concawe, 2013 Survey of Effluent Quality and Water Use at European Refineries, Report no. 12/18, Brussels, August 2018.
4. Concawe, 2013 Survey of Waste Production and Management European Refineries, Report no. 12/17, Brussels, November 2017.
5. Phillips P.S., Guide for Waste Minimization, University College Northampton, U.K. Lecture material presented on the GSCE Industrial Ecology seminar May 2000.
6. U.S. Geological Survey, National Minerals Information Center, Sulfur Statistics and Information, https://www.usgs.gov/centers/nmic/sulfur-statistics-and-information.
7. Market Watch, Press Release, $25bn Petcoke Market – Global Outlook & Forecasts 2018– 2024, February 26, 2019.
8. Fluor Corp., Fluor’s Guidelines on Sustainability Activities on Projects.
9. Profits with Purpose: How Organizing for Sustainability can Benefit the Bottom Line, McKinsey on Sustainability & Resource Productivity, July 2014.
10. Eccles, R.G., Ioannou, I. and Serafeim, G., The impact of a corporate culture of sustainability on corporate behavior and performance, Harvard Business School working paper, HBS Working Knowledge, No. 12-035, November 2011.
Author
Aad Zwaan is health, safety and environment (HSE) director at Fluor B.V. (P.O. Box 1381, 2130 EL Hoofddorp, the Netherlands; Email: [email protected]; Phone: +31 23 543 3028). Previously, he was employed by AVR, a major combustion facility for hazardous waste in the Rotterdam area. He has extensive knowledge of hazardous- and municipal-waste handling and treatment, including waste-to-energy processes. He graduated from the Technical University of Delft and specialized in HSE in design. He has been involved in petroleum refinery operations, petrochemical production and underground gas-storage projects worldwide, and has developed vast expertise in the evaluation of technical feasibility, front-end engineering design (FEED) and engineering, procurement and construction (EPC) packages with respect to HSE in design. Zwaan has more than 30 years of experience in the industry.