Advances in technology boost productivity and make today’s analyzers user-friendly
Between process-control optimization initiatives and increased environmental monitoring requirements, the number of gas analyzers in chemical-process-industries (CPI) facilities is proliferating at a faster rate than plant analyzer budgets and manpower can accommodate, according to industry experts. At the same time, a lot of employees with analytical expertise are retiring, so the analyzer knowledge base is shrinking dramatically.
To combat these challenges, chemical processors are upgrading older, maintenance-intensive gas analyzers with newer measurement technologies that require less maintenance and fewer support utilities. In addition to reducing maintenance and costs, upgrading to smarter, easier-to-use gas analyzers can provide quantifiable process benefits.
“Higher-performing analyzers often provide better repeatability, increased speed of response and better accuracy, as well as lower levels of detection, which can lead to significant gains in advanced process-control algorithms that ultimately lead to tighter process control,” says John Calame, product business manager for gas analytics, with Endress+Hauser (Houston; www.us.endress.com). “This tighter control drives improvements in product quality and reductions in off-specification product. These production improvements yield more sellable product at a lower cost and, therefore, higher profit margin.”
“Processors want the data and speed that only a higher-performing instrument can provide, so that they can respond to those data swiftly and with confidence in an effort to improve their product quality and reduce their costs, which drives their business forward,” explains Tracy Doane-Weiderman, marketing manager, analytics team lead for liquid and gas analytics with Endress+Hauser. “However, their focus is on their core business. They don’t want to spend a lot of time or effort gathering those data and tending [to] analyzers.”
For this reason, analyzers are becoming more robust so that they can withstand high temperature and corrosive environments, allowing them to be located closer to the measurement point. Placing the measurement device closer to the process measurement helps minimize sample transport time or, with some technologies, eliminate it completely, which results in faster, or realtime, measurements. The latest analyzers are also being developed to be more user-friendly, reduce maintenance time and cost, and provide flexibility.
Higher-performing analyzers
Some of the latest trends in the analytical world include optical techniques, such as tunable-diode-laser absorption spectroscopy (TDLAS) and Raman spectroscopy, which require very minimal support utilities. These technologies require very little or no consumables, such as carrier, fuel and calibration gases, and they minimize or greatly reduce the need for sample systems. They can also operate unattended for long periods of time, and often feature automatic validation to provide positive proof that the analyzer is working properly, so the operators are sure the instrument is accurate and calibrated, therefore they don’t dismiss alarms as nuisances.
TDL technology. TDL (tunable diode laser) technology has found applications in both process gas analytics and continuous emissions monitoring. The major benefit to this in-situ approach to gas analysis is that the measurement is performed non-intrusively and in realtime without any disturbance or delay to gas sampling or gas conditioning, says Warren Dean, strategic sales support for analytical products and solutions with Siemens Corp. (Alpharetta, Ga.; www.siemens.com).
In addition to accurate, realtime measurements, another major benefit is that the diode-laser measurement technology provides long-term stability through a built-in, maintenance-free reference gas cell, making field calibration unnecessary. “In many of the applications where TDLs are finding use, such as measuring ammonia in the stack, calibration is a nearly impossible task, but because these units have an internal calibration and internal reference cell, they don’t need to be calibrated in the traditional hands-on method,” says Dean.
Siemens’ LDS 6 can measure up to two components, including oxygen, ammonia, hydrogen fluoride, water, carbon dioxide, carbon monoxide and hydrogen chloride, and is component-specific from 0–5 parts per million (ppm) to 0–5 vol.%.
Another benefit of the in-situ approach provided by TDL technology is that, because it is applied directly in the process, it eliminates the additional steps of sample take off and sample conditioning required by more traditional measurement methods, says Jesse Underwood, product manager for TDLS analyzers with Yokogawa (Sugar Land, Texas; www.yokogawa.com). “This provides faster, actionable information because it removes the time and associated costs required with an extractive sampling and conditioning system,” explains Dale Cathey, analytical marketing manager with Yokogawa.
Yokogawa’s TDLS8000 TDL spectrometer (Figure 1) employs the company’s TruePeak technology, which can measure the area of the absorbance peak, eliminating effects from changing background gases and allowing for simple pressure and temperature compensation. And, its non-contacting sensor allows for use in corrosive, abrasive and condensing environments to measure O2, CO, CH4, NH3, H2O and more near-infrared absorbing gases. In addition, it offers a touchscreen and human-machine interface (HMI) to make it simple to operate and provide information, including trend graphing.
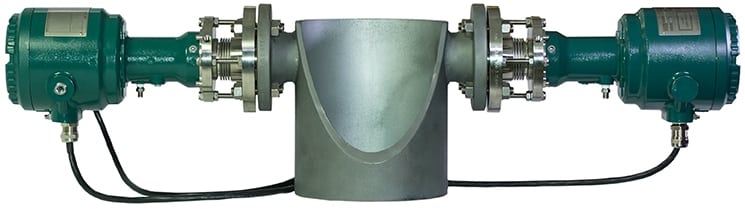
Figure 1. The TDLS8000 tunable-diode-laser spectrometer employs TruePeak technology, which can measure the area of the absorbance peak, eliminating effects from changing background gases and allowing for simple pressure and temperature compensation Yokogawa
Raman spectroscopy. Another current laser-based technology is Raman spectroscopy. In this technology, the analyzer produces spectra that resemble and can be analyzed like chromatograms, but they don’t require ovens, columns or use carrier gases. “The sensor itself is optically coupled via fiber-optic cables that go back to the base unit, so the technology doesn’t require a typical extractive sample, which eliminates the potential for fugitive emissions and quickens the response time,” explains Calame.
Endress+Hauser offers the Kaiser Optograf analyzer with Raman spectrography technology. This analyzer has multi-stream capability, with up to four probes per analyzer operating simultaneously, allowing up to four separate streams with multiple components per stream to be measured, as well as direct measurement of gas with a single analyzer. And, due to the fiber-optic coupling system, extensive extractive sample conditioning and sample transport infrastructure is minimized.
Ultraviolet (UV). UV analysis technologies also bring desirable features to the table, including increased reliability and advanced diagnostics that reduce maintenance requirements in demanding applications, such as tail-gas analysis, says Randy Hauer, product manager for sulfur recovery analyzers with Ametek Process Instruments (Pittsburgh, Pa.; www.ametekpi.com). For example, the company’s Model 888 sulfur-recovery tail-gas analyzer (Figure 2) uses UV technology to accurately monitor the H2S and SO2 concentrations in sulfur-recovery tail-gas. Model 888 provides reliability via automatic flow control for proactive response to adverse process conditions and flange temperature alarms for early warning of poor-quality steam, while smart diagnostic models identify, communicate and react to potential problems, which helps reduce unscheduled downtime.
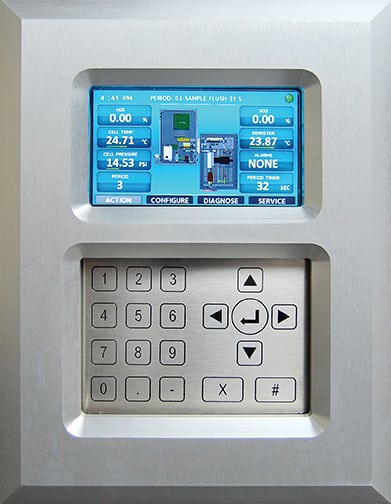
Figure 2. Model 888 sulfur-recovery tail-gas analyzer uses ultraviolet (UV) technology to accurately monitor the H2S and SO2 concentrations in sulfur recovery tail gas Ametek Process Instruments
Mass spectroscopy. Some of the latest, non-optical technologies also bring faster response times, increased reliability and flexibility to the table, notes Daniel Merriman, product manager for process analyzers with Thermo Fisher Scientific (Waltham, Mass.; thermofisher.com). “Some of the optical spectroscopy methods and lasers don’t support all of the applications that conventional process gas analyzers can,” he says. “Lasers tend to provide discrete measurements, but there are applications where multi-component measurements are required in different sample streams.”
For these applications, he says, being able to measure multiple streams with different gas compositions provides valuable and cost effective data at process control levels. However, even in these applications, processors are still seeking higher speeds. “Process mass spectrometers are generally capable of measuring complex gas-sample streams within cycle times that are ten to twenty times faster than traditional gas chromatographs,” says Merriman. “They are also largely configured by software so they are able to provide gas analysis from multiple sample streams where the gas composition might vary significantly between streams. Some of the processes being controlled are very dynamic so they benefit from fast gas analysis. That enables process control models to improve efficiency for the process that can yield increased productivity and reduced waste, resulting in reduced rework, reduced use of raw materials and lower energy costs. That’s really where the value proposition of these advanced technologies lies.”
The Thermo Scientific Prima PRO process mass spectrometer (Figure 3) was developed to provide faster, more complete, laboratory-quality online gas-composition analysis of multiple sample streams with different and varying compositions in each stream. The Prima PRO typically operates up to 90 days between calibration intervals, and it offers a fault-tolerant design for availability of greater than 99.7% to facilitate ongoing operation and enhance productivity.
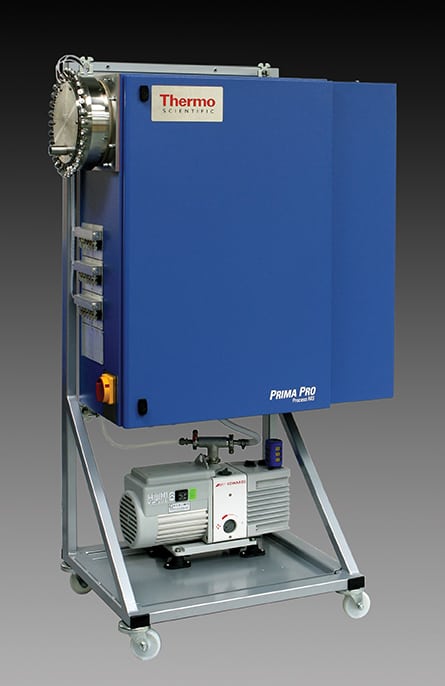
Figure 3. The Prima PRO process mass spectrometer was developed to provide faster, more complete, laboratory-quality online gas composition analysis of multiple sample streams with different and varying compositions in each stream Thermo Fisher Scientific
Improving gas chromatography
“While we are seeing requests for inline instruments and instantaneous measurements, there are certainly some obstacles to overcome with spectroscopy over gas chromatography,” notes Yokogawas Cathey. “Gas chromatography is extremely accurate because it measures the components directly, whereas spectrography provides an inferential measurement based upon the optical properties of what it is measuring. So, there are some cases where there are very good solutions for spectrometers right now, but they tend to be application-specific. What this means is that the gas chromatograph is still a very viable technology for large numbers of applications.”
Siemen’s Dean agrees: “Laser and other analysis technologies are not taking over the analysis market. So, for this reason, we are also working to improve our traditional gas-chromatograph technologies.”
He says a lot of effort has been made to improve reliability, stability and to include diagnostic systems that will recognize an issue or a potential problem. “There are now smarter sampling systems that can recognize issues like higher pressure differentials and that can constantly verify and validate measurements, as well as recognize when maintenance is needed,” says Dean.
In addition to these smarter systems, providers of gas chromatographs are working on ease of use and simplified maintenance, says Bonnie Crossland, product marketing manager for gas chromatographs with Emerson Process Management’s Rosemount Analytical (Irvine, Calif.; www.emersonprocess.com). “Gas chromatographs have never been viewed as an easy-to-use instrument,” she says. “So we are starting to work on ease-of-use with features like interactive and intuitive touchscreens and we now offer advanced diagnostics so the machine itself provides feedback and suggests preventative maintenance to correct problems before measurement errors occur.”
For example Emerson’s MON2020 gas chromatograph software makes configuration, maintenance, monitoring and control of a gas chromatograph easier with intuitive, Windows-based pulldown menus and fill-in-the-blank tables. The software collects and organizes the analyzed data from the company’s 700XA (Figure 4) and 1500XA gas chromatographs and gives management, operators, engineers and maintenance personnel access to critical data, such as current and archived chromatograms, alarm history, event logs and maintenance logs. It also allows users to check original calibration against last calibration and to perform operations checks and modifications simultaneously.
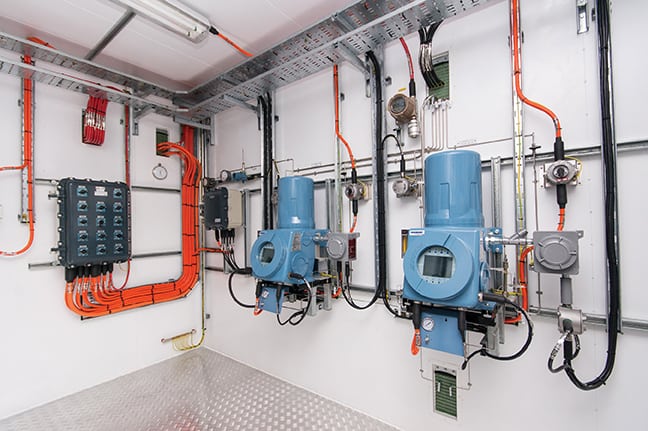
Figure 4. Gas chromatograph software control of a gas chromatograph is easier with intuitive, Windows-based pulldown menus and fill-in-the-blank tables. The software collects and organizes the analyzed data from gas chromatographs, such as the 700XA model shown here Emerson Process Management
“It allows users to get really specific and improve efficiency because they can get faster, more accurate results and adjust the process as needed based on the data, which results in more efficiency and less waste,” says Crossland. “It helps you make more of what you want to make and less of what you don’t and, because it is so intuitive and user friendly, you can accomplish this with fewer skilled experts.”
Providers of gas chromatographs also realized the maintenance process, too, needed simplification, so they are beginning to offer modular systems. Siemen’s MAXUM GC analysis platform offers a modular oven option, which is an airless oven design where complete chromatograph modules are snapped into place. Removal and replacement of a module can be performed in minutes, lowering operation and maintenance of the gas chromatograph. The module can then be repaired at the user’s convenience in their maintenance shop or returned for refurbishment.
Experts agree that it is more than likely that the improvements to gas chromatographs and other analyzers make upgrading a facility’s current technology worthwhile in terms of faster results, reduced maintenance time and costs, as well as improved process and product quality. “If processors haven’t looked at the newer technologies in the last five years and considered an upgrade, they should certainly give it a look,” says Crossland. ■