As the Covid-19 outbreak persists, the need for additional N95 face masks and other personal protective equipment (PPE) has been growing. Many companies are adding or augmenting production to facilitate increased PPE demand, including DuPont and Cummins; Porvair; ExxonMobil and many more.
At Purdue University (West Lafayette, Ind.), faculty and staff are organizing the production of much-needed medical supplies for Indiana hospitals. Because Purdue conducts research and teaches a variety of classes in manufacturing, technology and engineering, the university has several small manufacturing facilities. Capabilities include injection molding, vacuum forming, roll-to-roll manufacturing, machining, 3D printing, laser scanning and assembly operations. The medical supplies — safety glasses and face shields at first — are expected to be delivered to hospitals in Indiana this week.
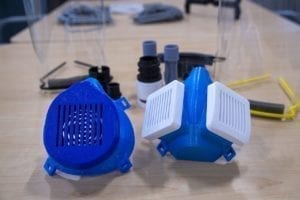
Nate Hartman and his team of Graduate students from Purdue use 3-D printers to manufacture PPE devices at the Indiana Manufacturing Institute, Purdue Research Park
For instance, Purdue’s Birck Nanotechnology Center is at work producing lenses for protective glasses and face shields in the center’s pilot-scale manufacturing facility. Currently the facility’s roll-to-roll laser cutting system has produced 1,600 lenses and 2,500 face shields, and is expected to eventually produce 3,000 lenses and 4,000 face shields.
Nathan Hartman, Purdue’s Dauch Family Professor of Advanced Manufacturing and head of Computer Graphics Technology, as well as co-executive director of the Indiana Manufacturing Competitiveness Center (IN-MaC), is leading the effort.
“Getting this done has been a lesson in persistence,” Hartman said. “Two weeks ago, when a few people began sending each other emails about discussing this, it seemed like it wouldn’t be possible. But people kept getting involved and offering their expertise and equipment, and within a week we began working on a plan, and now we have produced useful PPE for the health care community.”
Miko Cakmak, Purdue’s Reilly Professor of Materials and Mechanical Engineering, is overseeing the work in Birck. “A number of additional Birck staff members volunteered to work on this project to rapidly scale up our production,” Cakmak said. “The work is being carried out by staff scientists Guy Telesnicki and Nick Glassmaker.”
To support American response efforts, Honeywell (Charlotte, N.C.) is adding a face-mask production operation at its Phoenix Engines campus in Arizona. This location is one of Honeywell’s largest and has been dedicated to the design and manufacturing of aircraft propulsion engines and auxiliary power units since 1950. It will continue to manufacture this equipment, as well as produce PPE.
The Phoenix expansion, coupled with previously announced new production in Rhode Island, will allow Honeywell to produce more than 20 million N95 disposable masks monthly to combat COVID-19 in the U.S. Hiring is already underway for an estimated 500 or more new jobs in Arizona, which will bring the total between both operations to 1,000. The production will send masks to the U.S. Department of Health and Human Services.
In Korea, Toray Advanced Materials Korea converted its existing production line of materials for diapers into a filter production line for KF-80-class masks. It will produce 13-tons of mask filter-based non-woven fabric for 6.5 million masks a day.
While typical masks join the sponge-bonded non-woven fabric used in the outer and inner skin separately, Toray’s facilities have developed an independent process that combines the two non-woven fabrics in one line and makes them at once. Through this process, production speed is almost five times faster than facilities that produce only melt-blown products, which is expected to contribute greatly to resolving the shortage of masks.