The right mix of data collection, analysis, visualization and alerts can make the very daunting task of maintaining hundreds of pieces of equipment a simpler and more effective process
Chemical manufacturing is a labor- and capital-intensive process that is both controlled and restricted by various regulations. These regulations exist in part to address the hazardous conditions that can potentially be created as a result of operations. Manufacturers need to take precautions to prevent accidents, including actively maintaining high-performing and operationally efficient equipment.
Conscientious industrial building managers are now implementing preventative maintenance programs in an effort to proactively care for equipment and prevent failure. These programs can be costly and inefficient — making it challenging to justify the spend. For example, an engineer who prematurely changes a filter or a belt that has not met its full life wastes cost for the materials, as well as their time.
Maintaining equipment operations and performance doesn’t always need to come with these additional costs and time commitments. New tools, such as continuous monitoring and analytics solutions, are providing chemical manufacturers with visibility into their plant, giving them access to a more strategic and effective approach to equipment and operational management (Figure 1).
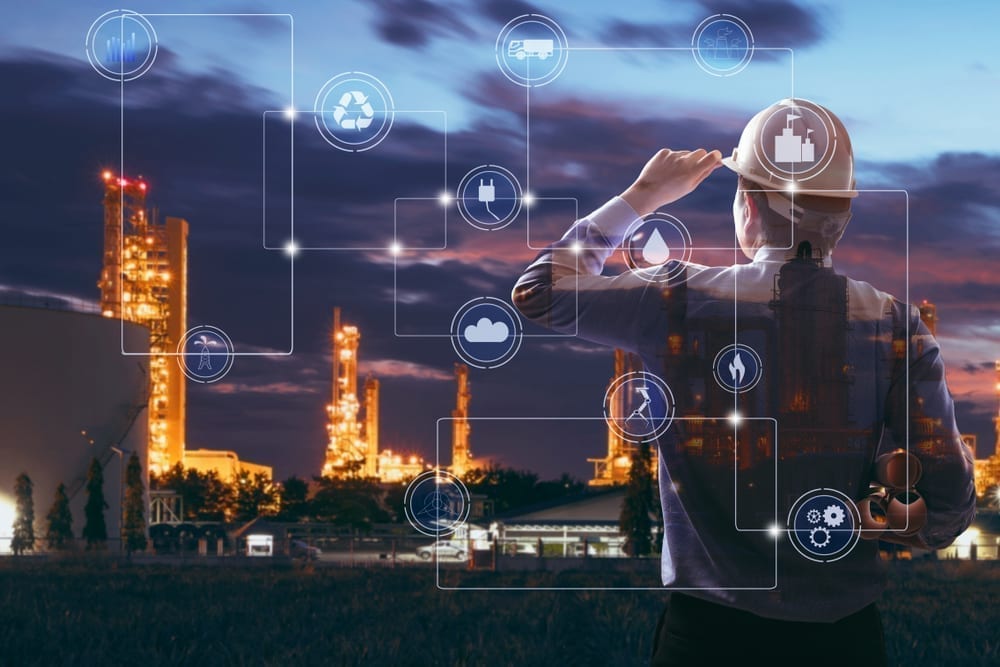
FIGURE 1. Bringing disparate data together via continuous monitoring can help engineers to better navigate the complexities of chemical processes
The complexities of operating a chemical manufacturing plant
Chemical manufacturers must be diligent across the entire manufacturing process to stay compliant and create a final, useable product. This process begins with managing feedstock (raw material) and a stream flow process to achieve either a chemical or biological transformation and/or a separation of materials. This process can include filtration, recrystallization (precipitation), settling (sedimentation), extracting (leaching), distillation, reverse osmosis, drying and adsorption.
Whether a chemical manufacturing plant moves fluids (gas or liquid) or solids (slurry), they all typically group equipment for a specific outcome into a unit. Each unit will be comprised of standard factory equipment and specialized process equipment to achieve various processes. On average, processes for a well-maintained fluid plant will perform at 90% capacity, and a slurry plant will achieve only 80% on average. Paying that 10–20% capacity penalty before processes become operational puts added pressure on ensuring manufacturing uptime.
Orchestrating a plant that meets all the operating demands is no easy balancing act. Plant operators must take into account operator safety requirements, productivity, costs and compliance with regulatory and manufacturing specifications. Increasing visibility within the systems and elements can help make the job easier and meet these operational and regulatory demands.
Interacting with your equipment
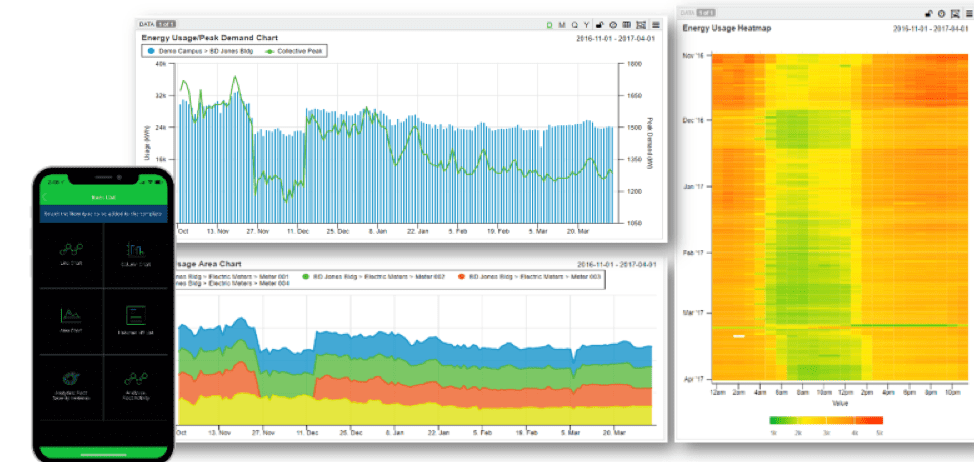
FIGURE 2. Energy and utilities management are among the many parameters that can be visualized via continuous monitoring and smart analytics
Introducing sensors and chemical analyzers can create transparency and help operators monitor control variables within utilities management, fluid systems, storage tanks and boilers or heat exchangers, as well as other equipment (Figure 2). Sensors gather raw data on many variables, such as temperature, pressure, flow and more, all of which can help to optimize process performance if plant operators are able to interact with and understand the data — which is not always the case. Continuous monitoring tools, such as monitoring-based commissioning (MBCx) platforms, have become readily available to interact individually with each piece of equipment, but very few are available to better coordinate these pieces of equipment and use the data to give clear directive and actionable feedback for process and system optimization.
Think of these technologies as an alarm — they can alert of an issue in a plant after it happens, but they cannot provide specifics on where the issue is, its severity, or provide advance notice that an issue may occur. This is why the industry is now seeing the integration of predictive analytics into continuous monitoring systems.
Using predictive analytics and intelligent alerts to understand equipment
Predictive analytics shift operations and maintenance from a reactive “fix-it” approach to a proactive strategy built on the data and voice of each piece of equipment. With this strategy, operators can tackle issues before they occur or escalate, saving them time, costs and headaches.
Predictive analytics work by analyzing equipment operating parameters in real-time to detect incremental trending that could indicate a failure. In many cases, simple corrective action or maintenance can be performed to avert a catastrophic failure that will inevitably lead to process downtime and added costs.
Being able to identify these operating conditions is not enough, however. Chemical plant operators need to be able to employ an intelligent alarm and notification system that brings these potential issues to the attention of the appropriate person. Furthermore, they need to alert the specific individual of the corrective action that is necessary to reduce downtime and fast-track issue resolution. All too often, real problems that are easy to fix get lost in the mire of noisy alarms in a facility.
It is not uncommon for there to be hundreds of alarms each day in a facility, making it easy for these significant indicators to get lost in the noise (Figure 3). It is nearly impossible to prioritize and focus efforts on the most important alarms through manual means alone.
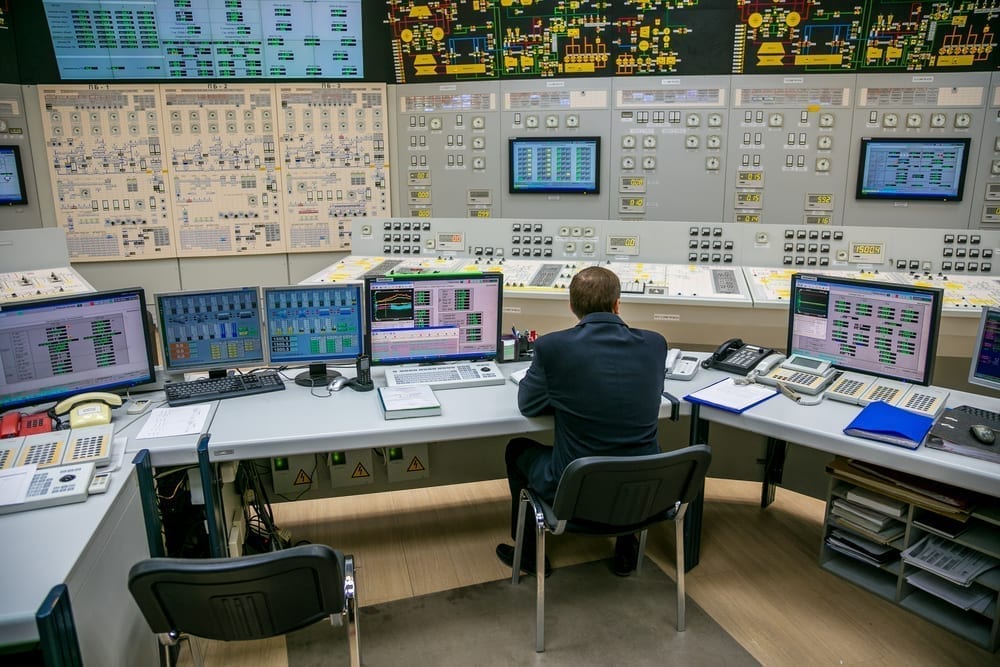
FIGURE 3. Operations personnel may be inundated with alarms throughout the day, and the capability to discern which ones are most significant is very valuable
Taking the sifting and sorting of the data out of the equation is what makes analytics useful for facility managers to proactively manage uptime. Instead of consuming hours of time to find out what happened or to look to diagnose a problem, the analytics serve up solutions and resolutions to the users. Using analytics as a tool to scrutinize the operating data of the equipment and combining these analytics with intelligent alarms to determine when action should be taken and what that action is key to creating this proactive approach.
Equipment failure prevention is just one benefit of using technology tools like continuous monitoring and analytics. These solutions can also be used to optimize utility efficiency and reduce wasteful consumption. Including addition data into the mix like meters for utility consumption like electrical, gas, water, air and steam can not only help identify excess consumption and peak, it can also help diagnose a piece of equipment.
With the ubiquitous use of electronic controls for equipment, it can be difficult and time-consuming to first identify if the condition is due to a mechanical failure, a problem with the controls, sequence of operations or code or an electrical issue. Using analytics allows for not only continuous monitoring, but also complex multivariable analytics in real time.
In any manufacturing facility there is no shortage of buzzers, bells, or alerts of some sort. The problem is identifying those alerts that are most important, not necessarily just urgent. To control the number of nuisance alarms, analytics can help prioritize based upon preventing failure, reducing utilities waste and process optimization. Creating intelligent alarms can notify not just the condition of the equipment, process or system, but also what information an operator may need to resolve the issue and where else in the facility this situation is occurring.
Setting parameters for operational and regulatory success
Oftentimes, equipment parameters for intelligent alarms are set upon the initial installation, but are not changed or re-optimized for new uses. These parameters need to adjust to cater to a number of different demands, such as environmental and regulatory requirements.
As products change, different environmental factors can impact both yield and product quality. For example, select chemicals may not be able to be manufactured well or at all in high-temperature, high-humidity conditions. Some products and clients require stringent control over the operating parameters to ensure high-quality products.
Another key operating parameter that can cause downtime is regulatory concerns. Compliance and regulatory matters typically require reporting of details about effluent, carbon emission or perhaps employee-safety considerations, like air quality in the facility. Being aware of the details that will keep a facility within select operating parameters are critical to establishing the visibility and providing the information needed to stay in compliance.
Better tools for data management
More data stored in a black box, from any data source, whether it is a machine programable logic controller (PLC), supervisory control and data acquisition (SCADA), a clipboard or an Excel spreadsheet, does not help maintain uptime in an industrial facility unless it is used to evaluate current operating conditions, set specific parameters and subsequently identify measures that can be taken to prevent failure, maintain compliance, reduce utility consumption and have a better understanding of overall capacity of the operations.
It is clear that continuous monitoring and analytics tools can offer great benefits, but it is also important for chemical manufacturers to understand the different solution offerings to determine which choice is right for each facility. On-premise solutions can require a massive amount of upfront time and labor to deploy. They can also offer the customization that may be required or desired. In addition, the ongoing need to support the deployment, administration and analytics development can be costly and difficult to find talent to handle, since it is a small but growing competitive space.
Cloud-based solutions, on the other hand, can offer industrial facility managers access to high-power analytics for commonly used industrial facility equipment like compressed air systems, boilers and chillers with no administration costs to manage. Solutions that offer connection to multiple data sources from multiple vendors can offer the most flexibility in correlating many data sources. The more data, the more vibrant the picture of the operation, the easier to pinpoint areas of concern.
Regardless of the solution deployed, chemical facility managers can customize the user interface of these technologies to collect, analyze and visualize data and alerts. Through visualization and representation of the data, insights become even clearer to maintenance and engineering staff who can better understand operations and opportunities areas to maximize uptime. This accelerates maintenance where it is needed and defers maintenance where it is not — freeing up staff members’ time to perform other work, as well as reducing costs by replacing parts before it is necessary. These visualizations also feed into maintaining regulatory compliance, and preservation of product quality.
Continuous monitoring, analytics and intelligent alarming tools can provide facility managers with the information they need in a timely fashion to act before their process or equipment fails. It is important to understand what elements of these solutions best support a chemical manufacturer’s unique needs and consider all aspects of the solution chosen to ensure it is the right choice. Can I collect data from the plant or field in real-time via a smartphone? Can I send alerts to ensure the right people know about conditions to be able to act in time? Can I create my own analytics with this tool? Can I tailor my user interface, per user? Do I have access control to safely allow access to the data but not open my process up to violation?
Once industrial facility managers have access to facility data, they can analyze that data, and correlate, aggregate and make better strategic decisions about plant operations. All data does not need to be analyzed to be useful. Sometimes data should just be presented to the right people in the right way at the right time. Using a combination of the right mix of data collection, analysis, visualization and alerts it can make what can be a very daunting task of maintaining the uptime of hundreds, if not thousands of pieces of equipment every day a simpler and more effective process. ♦
Edited by Mary Page Bailey
Author
Jennifer Grimley is the director of sales at FacilityConneX. She has over 20 years of experience leading regional and global sales efforts for industrial automation companies. Grimley has worked in a number of sectors within the industrial automation space, managing sales activity for industrial robotics in automotive, medical devices, plastic processing, life sciences, water and more. She has been working with clients to improve operational excellence, reduce waste, increase quality and equipment and process performance across many markets using many types of solutions.