Modular construction provides many benefits, but the decision to go modular should be thoroughly investigated
Modular construction, which includes projects from small- and large-scale process systems to pilot plants to entire modular facilities, is a growing trend in the chemical process industries (CPI). More than ever before, project owners are considering employing modular rather than traditional construction, because it often provides significant savings in schedule and labor costs. However, even though there are valuable benefits, modular construction is not suitable in every situation. This article discusses the advantages of modular projects, as well as provides advice on how to determine if a modular approach is the right the solution for your project needs.
Modular construction
Modular construction features complete units, prefabricated in a shop away from the plant site. The modules are typically built indoors in a controlled, assembly-line fashion and contain all the necessary components — including columns, reactors, heat exchangers, pumps and other process equipment, as well as instrumentation, piping, electrical wiring, lighting, control systems, safety showers and fire protection systems — all mounted within structural steel frames. Upon completion of the module or modules, testing of all components is performed at the shop and the modules are then transported, fully assembled, to the site, via truck or barge, depending upon the individual project size and location. The modules are lifted and set onto a pre-laid foundation and connected to each other, as well as to the plant utility piping and control systems (Figure 1).
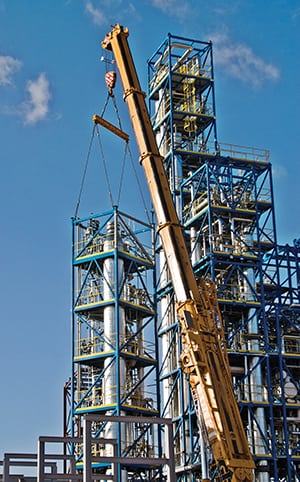
Figure 1. A lead crane lifts and sets one of approximately 20 modules comprising a reaction and distillation process to produce high purity chemicals for the electronics industry
Koch Modular Process Systems
Modular benefits
“Modular projects are becoming the norm and are considered a standard delivery option for construction projects,” says James Flake, director of operations, modular consulting, with Jacobs (Pasadena, Calif.; www.jacobs.com). “Just eight to ten years ago, we were one of only a few engineering, procurement and construction (EPC) firms bringing modular construction into the discussion. Now, our clients are modular-savvy and ask us to talk about them. We have a client who says their philosophy used to be, ‘Help me understand why we should use modules,’ but now jokes and says our job is to help them understand where they shouldn’t use modules.”
The reason for the shift in thinking is because modules, done correctly and for the right reasons, can provide several significant benefits (Figure 2).
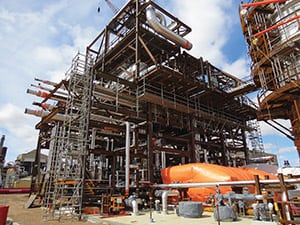
Figure 2. On the Shell Quest Carbon Capture and Storage Project in Canada (see also Newsfront on pp. 16–19), Fluor used its 3rd Gen Modular Execution approach to reduce the project’s plot space requirements, optimizing process block layouts and consolidating equipment into modules
Fluor
The most compelling reason to go modular, according to the experts, is the shorter schedule. According to Brian Loftus, vice president of business development with Koch Modular Process Systems (Paramus, N.J.; www.modularprocess.com), building a process module in a shop, with a well-controlled fabrication sequence, can save months when compared to traditional stick building methods outdoors onsite, where work is subject to weather-related delays, work permits, work stoppages or waiting for cranes and construction equipment. He says a typical schedule for delivery of a complete modular process unit, fabricated in stainless- or carbon-steel, is eight to nine months from the receipt of a purchase order, including all engineering and design activities.
Spencer Everitt, engineering manager with Xytel (Spartanburg, S.C.; www.xytelcorp.com), which builds modular pilot plants and commercial-scale units, adds that the compressed schedule provided by modular construction performed in a controlled-environment shop allows the project owner to bring product to market faster, which may also have major financial perks.
Building the modules offsite also results in minimal plant site interruption. In the case where a new process unit is being built alongside an existing operating unit, there may be hazards and safety risks associated with field construction activities, says Loftus. “It may not be safe to have contractors and construction workers walking around in a chemical plant, so often it makes sense to move construction off site to minimize the potential hazards and production interruptions,” he explains.
Everitt agrees that the modular model can significantly reduce plant shutdowns. “Because we are able to use really good three-dimensional technology and create very detailed laser drawings of where the module will be placed in a facility, we are able to build accordingly, then simply drop our modules in, plug them in and be out of the facility in four to five days, compared to the four to five months it would take to install the same project using traditional stick build. Again, there are financial benefits due to the reduced downtime.”
Another major benefit, according to Paul Hochi, director of project development, modular consulting, with Jacobs, is the predictability of modular projects. “The cost and schedule with a modular project tends to be less variable than with stick-built. I believe this is the most underestimated benefit in modular evaluations,” he says. The predictability of project cost and schedule is possible because of the nature of modular construction — there are no work stoppages due to permitting, labor or weather issues when work is performed in a controlled shop with skilled workers, notes Hochi. And, project quotes are usually done on a lump-sum pricing basis, so there are no surprises, says Loftus.
Loftus adds that single-source responsibility is another modular advantage. “The ability of one firm to provide all services from process design to pilot testing to construction enables our customers to benefit from a single-source supplier who can take responsibility for the overall process design, construction, integration, startup, commissioning and de-bottlenecking of the process,” he says. “This de-risks the project for the customer, while also reducing costs. With each layer of interface on a stick-built project comes more risk and more cost because each firm takes a profit along the way.”
Is modular the right choice?
While there are many advantages associated with modular projects, the experts will agree that modular is not always the right solution, and the decision to take the modular route should be business-based. “Before moving forward with a modular project, you need to be sure you can execute a modular job well and that the business case for executing as a modular project meets the project’s objectives,” says William Meyer, vice president, construction-modularization, with Fluor Corp. (Dallas, Texas; www.fluor.com). “In simplest terms, that means we are looking to determine if a modular project will be beneficial and, if so, the proportion of manhours we need to move offsite for the maximum amount of value, Meyer explains. “This will vary from project to project, location to location and from one timeframe to another. You can have an identical project in a different location or during a different timeframe and the feasibility study could yield a very different result, he says.
“When determining whether a modular solution is the wise choice, you need to come up with a balance,” Meyer continues. “If you’re looking at economics alone, you’re looking at a balance between moving manhours offsite into a more productive, more cost-effective location. On the downside, there will be additional costs associated with more detailed engineering work, more quantities of structural steel required, plus the cost of transporting the modules to the site and installing them onsite, to name the primary cost drivers for many projects. There comes a point in the equation where increasing the materials or the engineering hours or factoring the cost of transportation to move additional manhours offsite causes you to reach a plateau where the marginal benefit you achieve by moving manhours to the fabrication shop will be offset by the additional costs incurred to do so. You have to find the sweet spot for your project, meaning the appropriate proportion of work to include in your modular scope. Sometimes, the business case benefit may be dependent upon other factors, such as compressed schedule, reduced footprint or reduced loss of downtime.”
For this reason, Jacobs’ Hochi says it is important to take a “holistic” approach when considering a modular project. “Many of the benefits are direct to the project but some are advantageous to the business, as well, so we tell clients to also consider their business drivers when contemplating a modular project,” he says. “Perhaps they want the project up and running as quickly as possible so they can get product to market faster. Perhaps there’s a labor shortage in the area and they want to mitigate the risk of work stoppages by going modular. Increased safety related to taking the elevated work closer to grade in a fabrication shop may be another factor to consider.”
That said, there are certain challenges associated with some construction projects that typically make certain projects “good candidates” for modular construction, says Meyer. Situations that fall into this category include multiple large-scale projects in one region, which often results in a higher demand for construction resources in that area; a major project being built in a remote location where skilled labor productivity is a challenge and manpower is difficult to obtain; projects in areas that are subject to weather extremes such as a lot of snow, high winds or hurricanes; and projects that do not have a large “lay down” area where materials or construction crews and equipment can be placed and stored during a long-term project.
Because there are so many variables associated with the decision making process, Meyer has created a flow chart, shown in Figure 3.
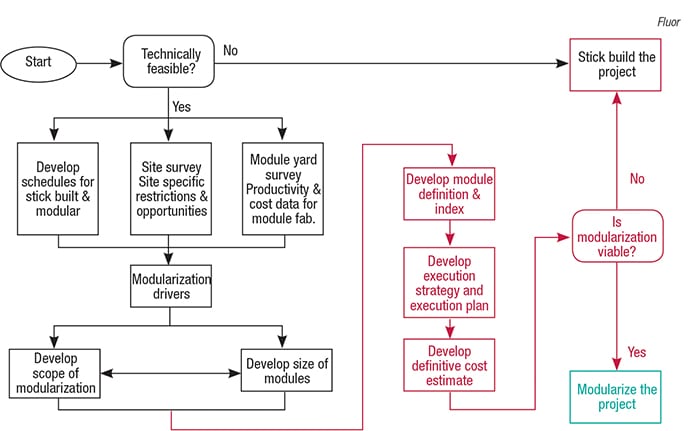
Figure 3. Using a flow chart such as this can help determine whether it’s economically feasible to modularize a project
Special situations
While modularization provides benefits for many projects, there are a few unique situations in which modular projects are especially attractive.
Onsite gas supply solutions.While modularization provides benefits for many projects, there are a few unique situations in which modular projects are especially attractive. For example, some CPI applications require continuous amounts of high-quality gases, which include O2, N2 and H2. However, since this is not their core business, many of these processors look for a supplier to manage the availability of these gases. The supplier will often install a modular solution onsite, which potentially eliminates delivery interruption, removes the cost of delivery and assures the processor of the reliability of supply. Linde LLC (Murray Hill, N.J.; www.lindeus.com) is one such company that offers onsite supply solutions.
Ecovar onsite gas supply solutions are modular supply systems built around standardized components to ensure maximum cost efficiencies and to assure quality of fabrication (Figure 4). Standardized design and dimensions help keep fabrication and installation costs low. These cost savings enable competitive gas prices to be offered to customers.
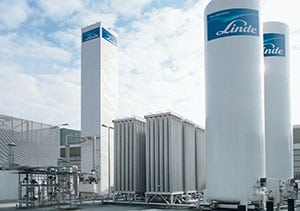
Figure 4. Modular gas plants, such as this Ecovar plant, are installed around the world for the dedicated production of oxygen, nitrogen, hydrogen or other industrial gases. Linde owns and operates the plants, monitoring and controlling production remotely. They deliver reliable, low-cost supply with no upfront investment cost, no overhead costs for labor, and no operating risk
Linde
Through the combination of standard modular onsite plants and backup liquid tanks, the Ecovar facilities offer solutions with minimal capital expenditure, low operating costs and low consumption of utilities, such as energy and water. Systems and system modules can be combined as required to create tailored solutions that suit local requirements, and the systems can be designed for indoor or outdoor installation to fit available space and utilities (energy, water and compressed air).
“There are several things that are attractive about this modular gas-plant scenario,” says Nick Onelli, conceptual engineering manager, with Linde. “A large H2-generating plant, for example, can take three to four months to install onsite via traditional stick-build, but these smaller, modular and compact plants can be installed in about a month. The overall time from release of plan to having an operating plant is reduced from 18 months to three years in a stick built project, to 6 to 15 months in modular construction. That’s a significant reduction in time and on-site risk.
“The other benefit is that the customer can concentrate on his core business because we offer a model where we build, own and operate the gas plant,” says Michael Barrasso, senior business development manager with Linde. “There isn’t a large investment in a gas plant, they don’t have to hire labor or maintain the gas plant and they receive a reliable supply of gas, much in the same way they would receive electricity from the utility.”
Developing technologies.Many developing technology companies are interested in working with modular process designers, says Loftus. “Often we start with these firms during the process development and help them evolve their technology from that stage into pilot testing. From there they want to deploy their technology to the marketplace and one of the options many now consider is to sell a complete packaged system to their customer rather than just selling a bundle of technology on paper. In these cases, we can help them design and construct modules so they can sell their technology as a modular process system to their end user.”
He says this business model benefits both the technology company and the end user. “The technology company can more easily leverage their IP [intellectual property] management because, if they sold the technology in paper format, it is easily disseminated and they lose control over how the technology is executed, but if the technology is sold as a complete package, it keeps the IP at home and they have more control over detailed engineering, which increases the quality control of the technology they are selling. In addition, the revenue proposition is often better,” Loftus explains. “The end user also benefits for the reasons anyone undergoing a modular project benefits — the construction schedule is compressed and the labor costs are reduced due to the efficiencies of modularization.
“This is really a unique application for modularization because there’s benefits for both customers.”