Digitalization, sustainability, security and safety are at the forefront of innovations in the logistics and supply-chain sectors
Ensuring that chemical products reach the correct location at the correct time requires intricate networks of complex logistics and scheduling tasks where several entities may hold a stake. Users are beginning to reap the efficiency benefits of adopting advanced automation technologies to streamline logistics activities, but concerns about security, infrastructure and an aging workforce remain.
Supply-chain safety and security
As with chemical manufacturing, safety and security measures play a crucial role once the product leaves the plant to be transported to a distributor or customer. For this reason, chemical distributors must work closely with government agencies to ensure proper oversight is taken to protect personnel and product integrity. In April, representatives from the National Association of Chemical Distributors (NACD; Arlington, Va.; www.nacd.com) visited Washington, D.C. to promote reauthorization of the Chemical Facility Antiterrorism Standards (CFATS) program, as well as advocate for freight rail reform. NACD has worked closely with the U.S. Department of Homeland Security on the CFATS program, which was first launched in 2007. “CFATS looks directly at chemical risk, and management of that risk,” says Douglas Brown, chairman of NACD and president of Brown Chemical Co. (Oakland, N.J.; www.brownchem.com). CFATS is predominantly oriented toward fixed chemical sites, but also requires facilities that transport any of the over 300 chemicals of interest regulated by CFATS to address chemical security issues. “CFATS enhances the safety envelope of the chemical industry from manufacturers down to distributors,” says Brown. NACD has also established its own program to address security and safety issues, Responsible Distribution. One element the program focuses on is carrier selection, which considers how to qualify third-party providers. “This has helped make the transportation of chemicals much safer over time,” Brown adds.
Driven by the lack of responsiveness on the part of the rail sector, NACD is pushing for better customer service and cost competitiveness from rail providers, explains Brown. Further compounding the rail-related concerns are several developments in the trucking sector that are impacting the trucking capacity available for chemical distribution. Typically, when distributors face issues with rail transport, they can turn to trucks as a reliable alternative. Now, however, as the trucking sector adjusts to new regulations designed to enhance safety and security, driver shortages are creating bottlenecks. “With the advent of more rigorous background-check requirements for truck drivers due to concerns about chemical safety and security, the result has been a decreased pool of available drivers,” says Brown. Furthermore, in April, federal mandates took effect that require drivers to use electronic logging devices, which hold drivers to new levels of accountability. Finally, Brown states that the aging fleet of drivers and the difficulty in attracting new drivers into jobs that require the transport of potentially hazardous materials are putting further stress on chemical distributors. “Driver shortage is a big issue,” he adds.
Digital evolution
Beyond physical security, cybersecurity is increasingly important as connected devices become more ubiquitous in trucks, trains and warehouses. Advanced telemetry and smart GPS devices provide information to distributors about the location and status of their fleet, while radio-frequency identification (RFID) and advanced barcoding technologies are contributing to more connected warehouses. While the NACD has begun early discussions about the potential use of autonomous vehicles, Brown emphasizes that they have not yet developed any official positions on the topic. “There are just so many variables and hazard scenarios that require driver interaction. But I’d imagine at some point, autonomous trucks might be utilized within the yards of large facilities or moving trailers back and forth into position,” he adds.
Smart wearable devices and augmented reality are two emerging areas of development for the logistics sector. Honeywell Safety and Productivity Solutions (SPS; Fort Mill, S.C.; www.honeywellaidc.com) offers voice-directed systems integrated into headsets that guide personnel through a set of complex, standardized tasks on checklists for preventive maintenance or inspection work. “This replaces paper-based work, which is prone to human errors and inefficiencies. The voice system guides users through their tasks and ensures compliance with documented workflows,” says Bruce Stubbs, Honeywell SPS director of supply chain industry marketing. Augmented reality is an emerging technology just beginning to find a place in the logistics sector, but Stubbs says it is most applicable for training workers. “The supply chain cannot necessarily move much faster, so companies are looking for ways to increase throughput and efficiency. But improvement can only happen when work is measured and data captured,” he continues.
The adoption of advanced technologies is essential for producers of hazardous chemicals or sensitive pharmaceutical ingredients, since products must meet stringent quality benchmarks and companies must comply with frequently changing government regulations. “The pressures for better transparency, accuracy, productivity and safety are driving the need for greater connectivity in the supply chain,” says Stubbs. “In Europe, for example, manufacturers of pharmaceuticals and other controlled substances, like explosives, are required to accurately track their shipments throughout the entire supply chain. They need to document each time a shipment passes through various stages or changes hands,” he adds. Honeywell SPS has developed cloud-based track-and-trace platforms that enable companies to track products — from an entire pallet down to a single item (Figure 1). “Each item receives a unique identifier, which is scanned and documented at each point in the supply chain, and this information is accessed from the cloud via a mobile device,” explains Stubbs. And when sensitive pharmaceutical products are transported, the truck itself can be monitored to ensure that shipments are not subject to conditions that could compromise product quality, such as exposure to excessive light or high levels of humidity. The system can even detect whether a truck stops unexpectedly or drives over uneven surfaces, which can jostle the shipment, resulting in bubbles that could damage the final product before delivery. According to Stubbs, AstraZeneca (Cambridge, U.K.; www.astrazeneca.com) has employed such advanced tracking capabilities across its global supply chains.
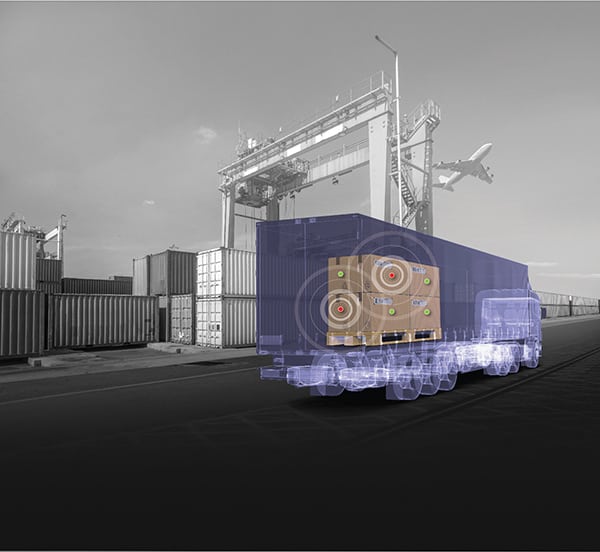
FIGURE 1. New track-and-trace capabilities enable precise monitoring of a shipment, pallet or even an individual item
Honeywell
Batteries power efficiency
One area of critical importance in logistics monitoring is the batteries that power a fleet of assets. Batteries must be properly charged and maintained to ensure continued high-performance operations. With this in mind, Ametek Prestolite Power (Troy, Ohio; www.prestolitepower.com) has developed the Insight cloud-based reporting tool that helps to manage battery-powered assets, such as forklifts. “The tool helps to identify maintenance needs and bottlenecks and makes data available remotely,” explains Jeff Harrison, business manager for Ametek Prestolite Power. “We have a device that we install on each battery that measures several aspects of the battery’s performance,” he continues. These measured factors include the battery’s temperature and whether the battery has been equalized and watered on schedule. Equalization is an important protocol for battery health and is typically completed once a week. Since most forklifts are powered by lead-acid batteries, proper watering is required to maintain the correct electrolytic levels within the battery. Not only does the system measure those key metrics of battery health, it also provides status data on how the battery is being used, how many hours it is in service and when it is idle and available to be charged. According to Harrison, a key benefit of having all of this information on hand is that it holds operations and maintenance personnel accountable. “Five years ago, this technology was unheard of. Battery health monitoring was still wired and was more time-consuming and costly.” As users’ analysis of data continues to evolve, Harrison sees great potential for predictive capabilities: “People can see where problems are before they actually kill the battery and impact productivity. We can actually predict when a battery is going to fail.”
Automation is another area where the logistics sector is set to experience a fundamental shift. “There has been a huge push in the industry for automatically guided vehicles,” says Harrison. The advent of operatorless forklifts certainly brings productivity benefits, but also introduces challenges. “We have to develop a battery charger that is capable of recharging without a person,” explains Harrison. Although automated forklifts are currently quite expensive, Harrison expects that users will experience a relatively quick return on investment due to efficiency gains.
Alongside digital monitoring and automation, another trend in forklifts is the use of lithium-ion batteries (LIBs). “Right now, probably less than 1% of all forklifts have LIBs, but I think that’s going to expand quickly as the costs come down, because there are so many benefits,” says Harrison. Compared to lead-acid batteries, LIBs require less maintenance, can charge faster and have double or triple the service life. However, Harrison mentions that LIB safety and end-of-life recycling options are major concerns.
At Achema 2018 (June 11–15), Stöcklin Logistik AG (Dornach, Switzerland; www.stoecklin.com) is introducing the world’s first LIB for forklifts designed for use in explosion-protection areas. The benefits of using LIBs are considerable, but explosion risks have limited their application. The new batteries were approved for use in Zone 1 (2G) gas atmospheres earlier this year, and the company expects to receive certification for use in Zone 21 (2D) dust atmospheres very soon. “Until now, lithium batteries were considered dangerous and unpredictable, and designing a battery for explosive areas was not considered practical because of the high risks,” says Jörg Backhaus, ATEX representative at Stöcklin Logistik. In developing their new LIBs, Stöcklin considered many factors to guarantee safe operations up to 300°C. They chose lithium iron phosphate as the cell material and evaluated a combination of cylindrical and prismatic cell structures and cathode and anode materials. Active balancing of the cell and thermal stability were also important factors. “There are standard safety systems, such as a current-interrupt device and a positive-temperature-coefficient function that prevent thermal runaway,” says Backhaus. In R&D tests, the company demonstrated that the explosion pressure of the batteries was extremely high — in some cases, 2–3 times the typical expected explosion pressure. The ability to achieve these explosion pressures led them to seek a patent for LIBs for potentially explosive areas.
According to the company, if proper handling procedures are followed, the batteries can be used for as many as 5,000 cycles. This longer service life translates into benefits for forklift drivers, in that fewer battery changes are required, reducing employees’ exposure to battery acids. Beyond forklifts, other potential areas of application for explosion-proof LIBs include the mining sector and in cleanrooms, where they eliminate the gas-release risks that go along with lead-acid batteries.
Supply-chain sustainability
Alongside efforts to increase efficiency, providers of supply-chain solutions are also looking for ways to make operations more sustainable. Sometimes, seemingly simple changes can realize substantial benefits. For instance, HOYER Group (Hamburg, Germany; www.hoyer-group.com) began offering tanks constructed of composite materials rather than stainless steel. According to HOYER Group, the first company to employ these composite tanks was BASF SE (Ludwigshafen, Germany; www.basf.com). The tanks are constructed of a lightweight composite material with thermal properties that reduce the heating requirements for tanks. “Due to the lighter weight of these tanks, 2,000 kg more of liquid chemicals can be handled within the defined payload of a transport, thereby reducing travel, costs and CO 2 emissions,” says Andreas Essinger, director of sales and business development at HOYER Group’s Chemilog unit. Reducing the number of trucks on the road is increasingly important as routes become more crowded and the pool of qualified drivers gets smaller. “Europe’s transportation infrastructure is congested. In some of the areas close to European chemical industry sites, traffic jams are increasing, which decreases productivity,” explains Essinger.
Ensuring that personnel are properly trained is another aspect of sustainability, especially in situations where hazardous materials are handled and transported. HOYER Group recently announced an expansion of its onsite logistics activities at the Shanghai manufacturing site (Figure 2) of Covestro AG’s (Leverkusen, Germany; www.covestro.com) Coatings Adhesives Specialties business unit. According to HOYER Group, while the logistics concerns of chemical manufacturers like Covestro are mostly similar to companies in other sectors, all workers must be rigorously trained to ensure optimal operations for both onsite and offsite logistics activities (Figure 3). “The product needs to be handled safely and carefully, the quality needs to be maintained and the logistics services need to be on time,” says Ulrich Grätz, global director of supply chain solutions at HOYER Group.
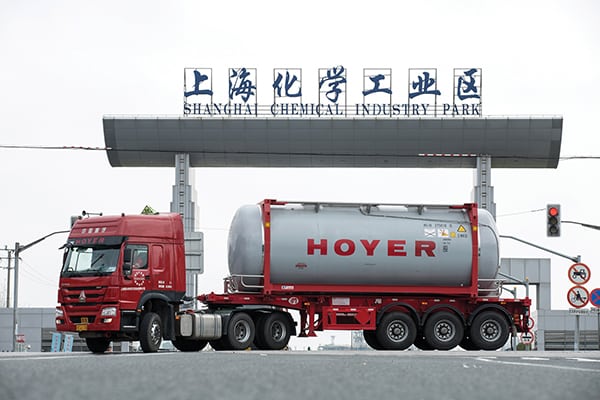
FIGURE 2. HOYER Group has expanded its onsite logistics activities for Covestro’s Coatings Adhesives Specialties facilities in Shanghai
HOYER Group
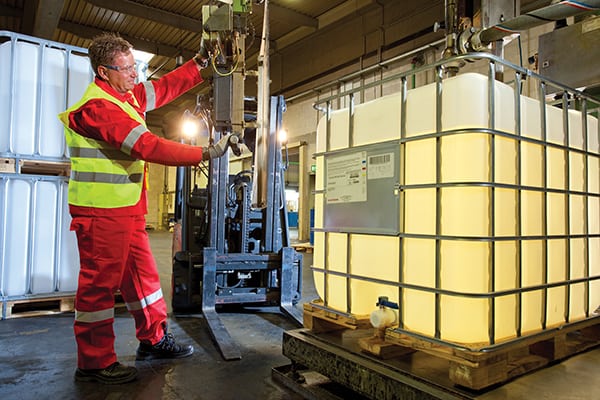
FIGURE 3. Logistics workers who encounter chemical products must be sufficiently trained in the proper handling techniques
HOYER Group