Thermal oxidizers can be used for the abatement of a wide range of air pollutants and volatile organic compounds. This article describes the custom design of a thermal oxidizer to treat three different waste streams from a biogas plant
A biogas company needed a treatment system for emissions abatement of volatile organic compounds (VOCs). The system would be installed downstream of a pyrolysis furnace and multiple condensers in order to thermally oxidize three waste streams high in sulfur and nitrogen concentration, while also limiting the formation of oxides of nitrogen (NOx). A custom proprietary system was designed, engineered and fabricated by Ship & Shore Environmental (S&SE; Signal Hill, Calif.; www.shipandshore.com) to meet this plant’s unique specifications.
The system
The main distinguishing characteristic of thermal oxidizers is that they do not rely on direct ignition of the process gas for oxidation. Rather, they sustain the correct combustion conditions by maintaining an operating temperature sufficiently above the auto-ignition point by providing enough time for combustion and by the presence of excess oxygen to complete the oxidation reactions.
The multi-stage thermal oxidizer system designed by S&SE (Figure 1) needed to operate under vacuum in order to pull a vacuum on the pyrolysis reactor and provide the motive force for the flow of the produced gas from the pyrolizer (Stream 1) to the thermal oxidizer. Streams 2 and 3 are supplied to the thermal oxidizer through positive-displacement pumps. The induced draft/vacuum was designed to sufficiently pull all of Stream 1 into the thermal oxidizer to maintain a proper vacuum at the Stream 1 connection point. The plant’s waste streams contain sufficient nitrogen content that if directly oxidized in a standard thermal oxidizer, an excessive amount of NOx would form. Thus, in the new thermal oxidizer unit, the streams are burned in a staged operation where the initial stage is a high-temperature reducing (oxygen-starved) atmosphere. The high temperature and more than 1-s residence time assure dissociation of organic compounds. Since combustion of the waste streams is exothermic, the process uses virtually no natural gas, except during startup, which greatly reduces costs. The exhaust gas from this initial stage contains an excess of combustible compounds, primarily carbon monoxide, and hydrogen. This reducing atmosphere provides proactive control of NOx, as bound nitrogen compounds are converted to diatomic nitrogen (molecular N2) instead of NOx.
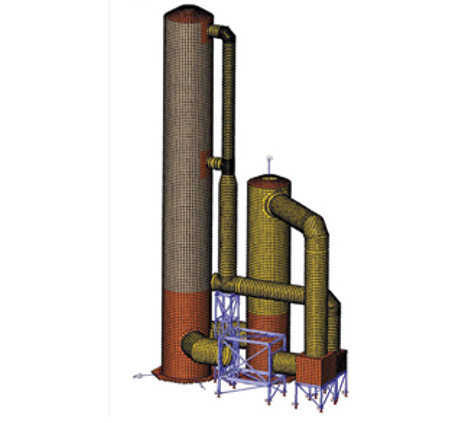
FIGURE 1. A customized thermal-oxidizer system was designed to handle the contents of three distinct waste streams from a biogas pyrolysis unit
There are typically two primary processes for the subsequent stages in a multi-stage thermal oxidizer. One process uses two additional stages (for a total of three stages). The initial stage is the reducing stage. A second reducing stage occurs in the thermal oxidizer (second chamber), which is still in a low-oxygen environment with a temperature of about 1,650°F to prevent excessive NOx formation. Following this stage, the fluegas enters the cool-down process. The cool-down process is split into two outlets, with one outlet going through the quench phase, while the second outlet is going through a heat exchanger. The second outlet can be used to increase the inlet temperatures (Streams 2 and 3), or to recover heat that can be used anywhere else in the plant.
Such a system, defined as a low-NOx thermal oxidizer, is not designed for 100% NOx destruction, but combining it with a selective catalytic reduction (SCR) system can eliminate the production of NOx. Limited space and potential excess production of NOx due to waste streams high in nitrogen provided unique challenges for the engineering team at the biogas plant.
S&SE designed the system vertically to fit into the limited space available at the site. One of the advantages of the vertical-system configuration and its down-fired burner is that any possible effect of ash or particles on the burner was eliminated. Simultaneously, the plant does not need to use any natural gas for combustion, which significantly saves on costs. Finally, the heat exchanger allows the plant to utilize a significant amount of heat elsewhere in the plant at no additional cost.
Author
Anu D. Vij is chief operating officer (COO) of Ship & Shore Environmental, Inc. (2474 N. Palm Drive, Signal Hill, CA 90755; Phone: (562) 997-0233; Email: [email protected]; Website: www.shipandshore.com). Vij has over 20 years of experience in the environmental, chemical, petrochemical and air-pollution control industries, and has specific expertise in thermal oxidation technologies. As COO of Ship & Shore, he oversees several business units, including Sales, Finance, Engineering, Project Management, Procurement, Production and Services. Prior to joining Ship & Shore, Vij served as vice president, enclosed combustion systems, at Aereon, and was director of engineering at OnQuest, Inc. Vij holds a M.S.Ch.E from University of Southern California, and a B.S.Ch.E from Panjab University in India.