Industrial manufacturers across the globe are responding to the COVID-19 global pandemic by modifying their production capabilities to produce crucial supplies, including essential personal protective equipment (PPE). Companies contributing their manufacturing capabilities and expertise to provide PPE include Honeywell and Toray; DuPont and Cummins; Porvair; Materialise; DSM and Praj; Rohm; Invista and many more.
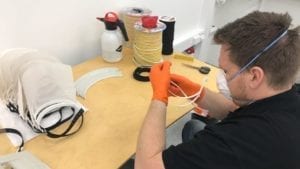
TechnipFMC is applying its 3D-printing capabilities to manufacture PPE
TechnipFMC (Houston) is helping protect medical workers during the COVID-19 outbreak by using 32 3D printers to produce visors at its facilities. The Edvard Grieg Project team prototype medical visor was approved for use in Norway, and 500 are on their way to Kongsberg and Drammen hospitals. Visors developed and printed by TechnipFMC’s teams in Brazil are being used by front-line hospital staff in Rio, while 3D printers at other locations, including Dunfermline in the U.K. are also joining the effort.
Dräger Inc. (Telford, Pa.) will also increase its production capacities supply N95 respiratory protection masks in support of efforts to fight the COVID-19 pandemic in the U.S. The U.S. Department of Health and Human Services (HHS) issued an award to Dräger for the supply of National Institute of Occupational Safety and Health (NIOSH) approved N95 respiratory protection masks. As part of the contract, Dräger plans to increase U.S. domestic production of the masks and expand its manufacturing footprint over the course of the contract.
Pump manufacturer Grundfos has modified production at its facility in Bjerringbro, Denmark to deliver up to 5,000 face shields per day to aid Danish health services in the fight against coronavirus. A key factor in developing the visor was making it easy to manufacture and easy and convenient for staff to use. The mask consists of a normal sheet of A4 foil attached to a plastic frame, which was 3D printed in the early stages of the project but now ready for production in a regular plastic tool.
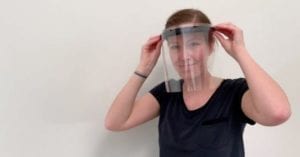
Grundfos is producing PPE components for donation in Denmark (Source: Grundfos)
“We have applied a standard product like A4 foil, so the visor is easier to produce. You simply make holes is the foil with a regular hole punch and then click it onto the frame,” explains Torben Buch Rasmussen, who leads the team behind the visors made for mass production.
“It is very important for our company to take social responsibility. We can help produce something, which is a deficiency, and this is not something we have to make money from. It’s just an attempt to help,” he adds. It is planned that Grundfos will join a taskforce coordinated by the Confederation of Danish Industry. Within this framework, several large Danish companies will develop parts for pharmaceutical equipment that may be missing from the Danish healthcare system. Lars Frelle Petersen, Deputy Director General of the confederation, is impressed with the efforts.
“We have now received inquiries from 170 companies that will attempt to assist with protective and medical equipment. Grundfos and other private companies display a truly unique commitment to society. Many are already squeezed by the crisis on liquidity and staffing, and we all face an uncertain financial future, yet these companies are stepping up,” he says.
The University of Idaho has devoted resources to manufacture face shields to protect workers from splatter and spray of coughing patients, as well as surgical masks, which have either been 3D printed or sewn from cloth.
UI mechanical engineering professor Gabriel Potirniche, who is coordinating these projects, said the face shield is essentially a barrier made from transparent plastic that covers the face from forehead to chin and is mounted with a strap that goes around the head. He said the shield itself can be laser-cut from sheets of plastic, but other pieces of the design must be 3D printed, which is more time-consuming.
“It takes about an hour and a half for each of the headband pieces to be printed,” Potirniche said. “However I would estimate that in the next week or so, if we have many printers working on these, we will be able to make many of them and deliver them to hospitals.”
Potirniche said multiple hospitals have expressed interest in the shields and in a plastic, 3D-printed mask design they have been perfecting as well.
He said these were originally based on a design they’ve dubbed the “Montana mask” created by a dentist in Billings, Mont. That design is essentially a plastic face covering resembling a dust mask with a small window on the front where a filtration medium, like surgical-grade fabric, can be placed. They have since widened that window to help users breathe through them more easily. This also cuts down on materials needed and printing time, Potirniche said.
Polymer processor Polyzen, Inc. (Apex, N.C.) is leveraging its expertise and innovation in material science, plastic processing, and product development to rapidly create the raw materials and products needed to protect front line healthcare workers. Already, the team has developed medical-grade, personal protective gloves. These gloves are produced to meet user durability needs, including leak, puncture, abrasion, and chemical resistance. In addition, these gloves are developed for use in critical environments that require barrier protection.
Polyzen is also actively working with other manufacturers, universities, and the state of North Carolina on products such as face shields, face masks, ventilator bags and balloons, bed tents for patient transport, and other single-use disposables to assist in protection and sterility.
“We are grateful to be considered an essential manufacturer for our existing medical device customers, and believe it is our ethical and professional duty to help during this dire need. We are humbled and ready to work hard to save lives,” said Sunil Inamdar, Polyzen CTO.